PCB met CNC (deel 1): Hoe frezen we printsporen in plaats van ze te etsen
op
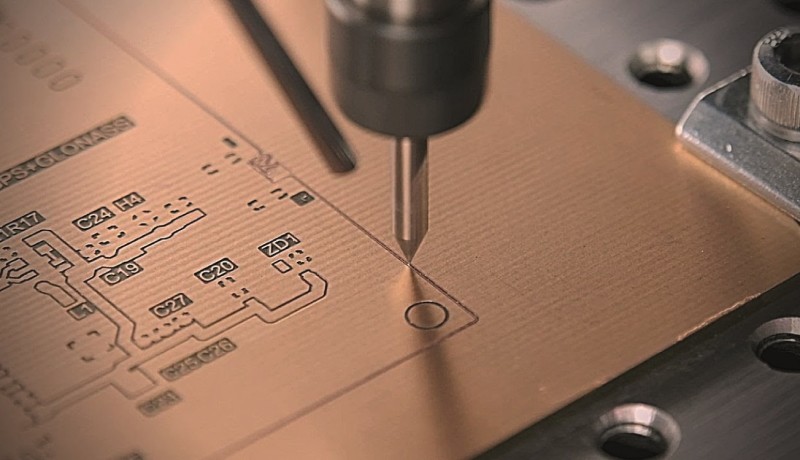
Voor prototyping of productiedoeleinden in zeer kleine volumes kan het gebruik van externe PCB-fabrikanten duur worden of op zijn minst een tijdrovende procedure zijn. Om verschillende redenen kan chemisch etsen niet praktisch zijn. In deze gevallen kan het CNC-frezen van een print als een goed alternatief worden beschouwd vanwege de nauwkeurigheid, het gebruiksgemak en, het allerbelangrijkste, omdat het een snelle manier is om een print klaar te krijgen waarmee we gelijk met solderen kunnen beginnen!
Iedereen die zich bezighoudt met praktische elektronica, of het nu voor zijn plezier is of voor zijn werk, komt vroeg of laat de noodzaak tegen om een print te maken. Prototypes worden gemaakt met breadboards of gaatjesprints, maar dit zijn bijna altijd schakelingen die moeilijk als definitief zijn te beschouwen, hoewel sommige mensen erin slagen om goed afgewerkte ontwerpen te maken met deze middelen. De weg van prototype naar definitief product gaat via een PCB (Printed Circuit Board), die meestal door een professioneel bedrijf wordt gemaakt, met kosten die tegenwoordig min of meer binnen het bereik van elke portemonnee liggen. Maar deze procedure is een optie voor een definitieve schakeling, die alle tests heeft doorstaan en misschien in productie moet gaan, zelfs voor kleine hoeveelheden. Als je echter in de ontwerpfase bent, het experimenteren een stabiele schakeling met een massavlak vereist, en je verwacht wijzigingen aan te moeten brengen na het testen, dan zijn de kosten van een professionele printplaat het misschien niet waard.
Tot een paar jaar geleden was de enige manier om een zelfgemaakte print te maken het ontwerp van de schakeling op printmateriaal over te brengen door middel van een fotografisch proces of toneroverdracht, en dit vervolgens in ijzerchloride (of andere geschikte chemicaliën) te dompelen om overtollig koper te verwijderen. Maar terwijl een schakeling in SMT (Surface Mount Technology) op dat moment klaar zou zijn, als we het over THT (Through Hole Technology) hebben, was de tweede stap die moest worden uitgevoerd het boren. Hier begonnen de problemen omdat, zoals we allemaal weten, de gaten niet allemaal dezelfde diameter hebben en daarom verschillende boren vereisen, om nog maar te zwijgen van de noodzaak om elk gat precies te centreren. Het is duidelijk dat deze stap een aanzienlijke tijdverspilling betekende, met resultaten die zelden perfect waren. Deze technieken worden vandaag de dag nog steeds gebruikt omdat de stappen tot aan het etsen in ijzerchloride snel zijn en goede resultaten geven. Het omgaan met chemicaliën in kleine ruimtes, zoals een kamer thuis of een klein laboratorium, kan tamelijk gevaarlijk zijn.
De komst van CNC frezen, die nu overal verkrijgbaar zijn omdat ze steeds betaalbaarder worden, heeft zeker een revolutie teweeggebracht in de prototyping wereld. Ze maken het mogelijk om technisch perfecte schakelingen te maken, zonder met chemicaliën om te hoeven gaan en, het allerbelangrijkste, om perfect gecentreerde gaten van de juiste grootte te verkrijgen. In deze serie artikelen zullen we deze uitstekende combinatie gebruiken, samen met een verscheidenheid aan open-source of gratis software, om te leren hoe we een doorsnee printplaat kunnen maken met PTH-componenten. We zullen dan alle stappen zien die nodig zijn om het bestand te verkrijgen dat de CNC-frees zal aansturen voor zowel de frees- als de boorfase. Daarnaast zullen we een eenvoudige mechanische toevoeging voorstellen waarmee de te bewerken print met groot gemak en precisie aan de grondplaat kan worden bevestigd.
De programma's die we hebben gebruikt zijn: gratis Eagle 9.6.2, om de Gerber-bestanden te genereren, en open source FlatCAM v.8.5 hier te downloaden, dat zal worden gebruikt om de CAM-bestanden in G-code te transformeren. Deze wordt gebruikt door Candle v.1.1.7, ook open source, dat je hier vindt, dat zal zorgen voor het aansturen van de CNC-frees door de nodige commando's te geven aan de Controller. Autodesk's Eagle programma is niet open source, dus je moet het downloaden, en je vervolgens registreren op de website om het als een gratis versie met beperkte functies te kunnen gebruiken. We gaan er echter van uit dat het schema en de PCB lay-out al zijn gemaakt. Daarom zullen we direct bespreken hoe we de Gerber bestanden kunnen genereren. Dit betekent dat als je andere CAD-software hebt, je alleen de Gerber bestanden hoeft te maken en direct naar de tweede stap kunt gaan, die van CAM.
DRU-controle
Eerst moet je het schema en de print lay-out tekenen. Behalve in zeer zeldzame gevallen is het altijd handig om de print te voorzien van het zogenaamde "grondvlak", dat alle massapunten van de schakeling verbindt zonder de overeenkomstige sporen te hoeven tekenen. Dit vult ook alle lege ruimten van de printplaat op, wat erg handig is voor het frezen. Anders zouden we ons leven bemoeilijken door al het overtollige koper te moeten verwijderen, wat de tijd voor het frezen onevenredig zou verlengen. Als voorbeeld gebruiken we de tekening in figuur 1.
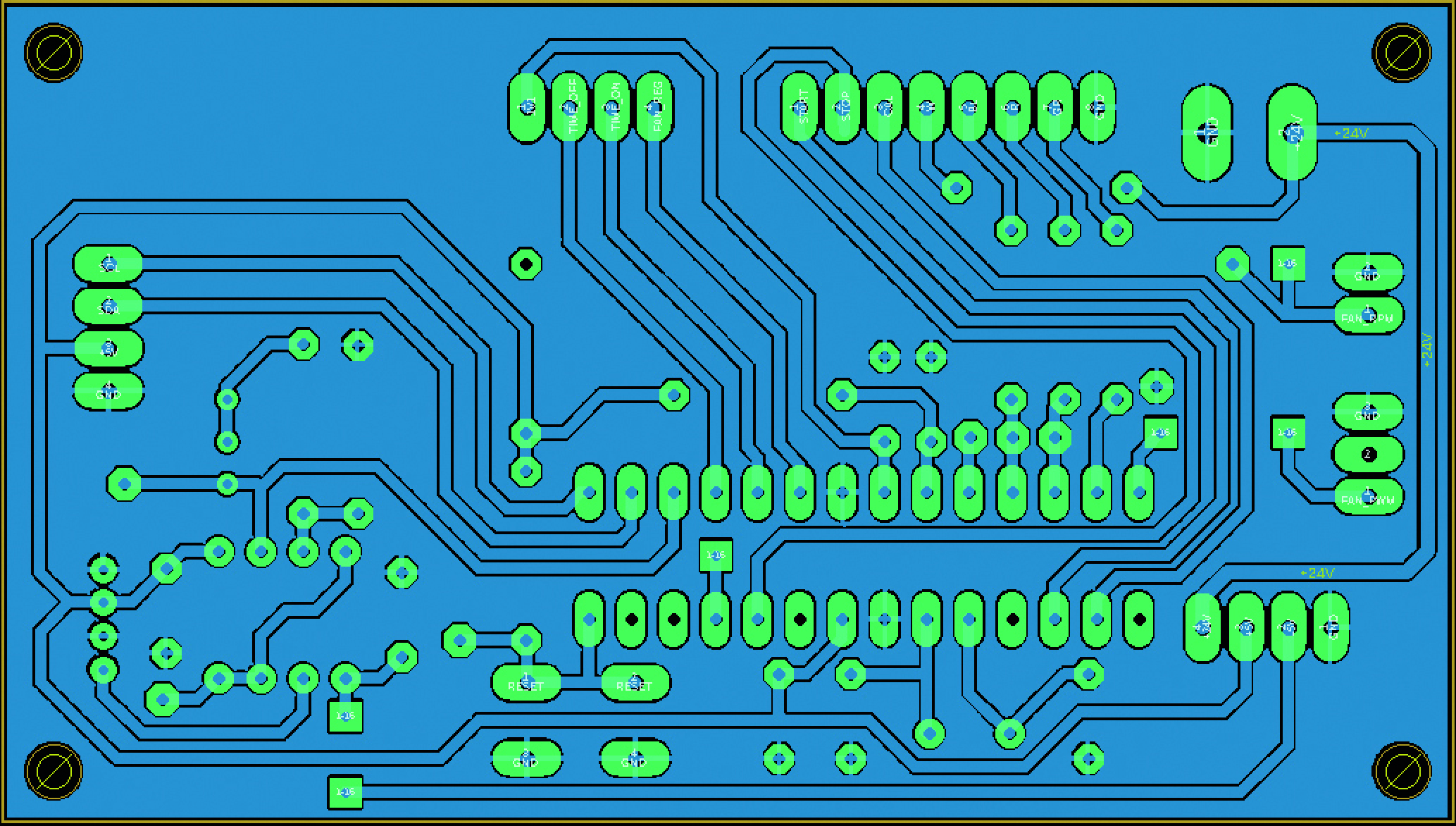
De eerste taak die moet worden uitgevoerd met het CAD-programma is het maken van een specifiek DRU-bestand (zo wordt het genoemd in het geval van Eagle) dat de ontwerpregels bevat, in principe de afmetingen van de sporen en de aansluitpinnen en hun tussenruimte, in overeenstemming met het type print dat moet worden gemaakt. Men moet er inderdaad rekening mee houden dat de typische standaardinstellingen van CAD-programma's prima zijn voor PCB-fabricage bij een professioneel bedrijf, maar niet voor handgemaakte prints. De parameters waarmee rekening moet worden gehouden, zijn in feite de minimumafmetingen van de aansluitsporen, pads (soldeerpads van de aansluitingen van de componenten) en vias (aansluitingen tussen boven- en onderkant van de print). Vervolgens de afstanden tussen de componenten onderling en tussen de componenten en het massavlak, d.w.z. al het aangrenzende koper dat de resterende ruimten van de printplaat bedekt en dat aan massa ligt. Als de juiste waarden niet worden gedefinieerd, kan het moeilijk zijn om componenten op de print te solderen. Laten we eens kijken naar deze parameters en welke waarden geschikt zijn om eraan toe te kennen:
- Clearance: is de minimale afstand tussen de verschillende onderdelen van het ontwerp: sporen, pads en vias. In ons geval gebruikten we een waarde van 8 mils, gelijk aan ongeveer 0,2 mm, wat een standaardwaarde is die ook gebruikt wordt bij productie. Dit betekent dat je vrij handig moet zijn met de soldeerbout, anders kan soldeertin tussen aangrenzende sporen, pads of het grondvlak kortsluiting veroorzaken. De waarde van 0,2 mm komt overeen met de grootte van de punt van de frees die we gebruiken met onze CNC-machine, waarmee een doorgang genoeg is om overtollig koper van de koperplaat te verwijderen tijdens het frezen (figuur 2). Als je denkt dat je niet voldoende soldeervaardigheid hebt, dan raden we je aan om deze waarde te verdubbelen tot 16 mils; in dit geval kun je een 0,4 mm frees gebruiken of de 0,2 mm frees, waarmee de CNC-frees twee aangrenzende doorgangen moet maken. In ieder geval kan het gebruik van vloeimiddel een goede hulp zijn bij het solderen door het met een kwastje aan te brengen voordat je gaat solderen. Dan kun je gemakkelijker solderen en wordt voorkomen dat soldeertin in aanraking komt met naburige sporen of pads.
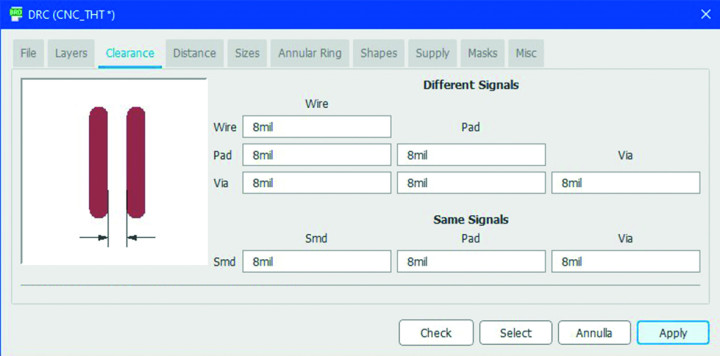
- Sizes: dit zijn de minimale afmetingen van de sporen en de minimale diameter van de gaten; door een te kleine waarde voor de spoorbreedte te gebruiken, loop je het risico dat een braam van na het frezen extreem dunne of zelfs gebroken sporen veroorzaakt. Wij gebruikten 24 mils, gelijk aan ongeveer 0,6 mm, terwijl de diameter van de gaten hier irrelevant is, maar een waarde van 16 mils is goed (Figuur 3).
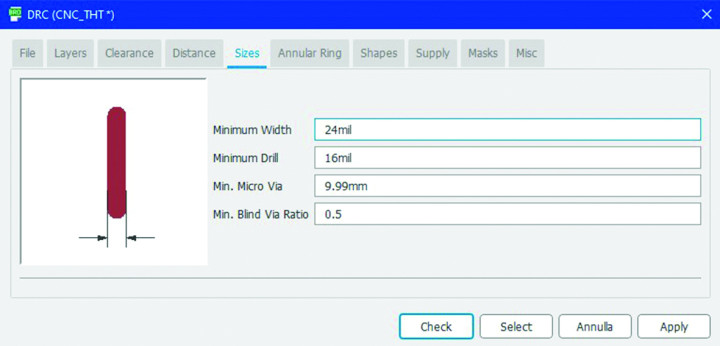
- Annulaire ring: dit zijn de afmetingen van de pads en vias; de standaardwaarden uit de bibliotheken van de verschillende componenten zijn goed als de print geëtst moet worden, maar als er met een CNC-frees gewerkt wordt, verliest de buitenrand gemakkelijk wat materiaal, terwijl boren zonder metallisatie meer materiaal in het centrale deel verwijdert. Dit kan leiden tot een te grote verkleining van de soldeerruimte rondom de pads, met de moeilijkheden die daarop volgen. De afmetingen worden gedefinieerd als een percentage van de binnendiameter van het gat, binnen een minimum- en een maximumwaarde. Voor pads kunnen deze waarden afzonderlijk ingesteld worden voor de boven-, onder- en binnenvlakken van de print, maar deze laatste waarde is irrelevant omdat ze alleen gebruikt worden voor professionele meerlagige PCB's, die niet realiseerbaar zijn met ambachtelijke technieken. Voor vias zijn de afmetingen uniek voor de twee buitenste vlakken, terwijl voor de binnenwaarde hetzelfde geldt als voor pads. Microvia's vallen ook onder de professionele types. In ons geval stellen we een maattoename van 50% in vergeleken met de componentenbibliotheken, met waarden tussen 10 en 40 mils (Figuur 4).
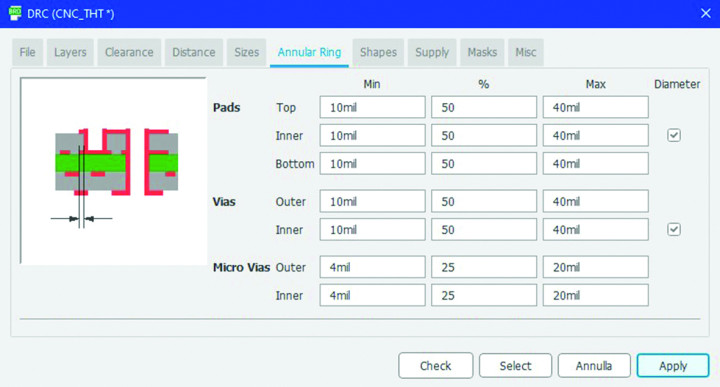
Je vindt he CNC_THT.dru bestand hier: How To Mill Your PCB Tracks Instead Of Etching Them"], dat gekopieerd moet worden naar de dru map in Eagle. Zodra je het PCB-tekenbestand hebt geopend, moet je het menuTools-DRC… gebruiken, op de Load… knop klikken en het bestand laden. Door eerst op Apply en dan op Check te klikken, zal Eagle de instellingen toepassen en vervolgens controleren of de lay-out overeenkomt met de instellingen in de DRU, zo niet, dan wordt een venster geopend met alle gevonden fouten. In Figuur 5 hebben we opzettelijk een DRU voor CNC-frezen toegepast op een PCB-ontwerp dat gemaakt is voor fabricatie in een productiebedrijf. Het resultaat is 387 fouten en 30 waarschuwingen. Specifiek hebben we:
- 31 Clearance: betekent dat in 31 gevallen de minimumafstanden tussen sporen niet werden gerespecteerd.
- 1 Drill Size: betekent dat de grootte van een gat in één geval kleiner is dan de minimaal toegelaten grootte.
- 5 Overlap: betekent dat er vijf problemen zijn met overlappende sporen, doordat de gebruikte DRU-instellingen de pads groter maken en ze met elkaar overlappen; eigenlijk zou deze fout zelfs optreden met de juiste DRU; we hebben ze zelfs opzettelijk veroorzaakt.
- 350 Width: betekent dat de sporen in 350 punten niet voldoen aan de minimumgrootte die is ingesteld door de DRU.
- 30 Wire Stub: dit zijn herhalingen op sommige plaatsen van de sporen. Het gebeurt gemakkelijk wanneer we een spoor wissen om het opnieuw te maken, maar we realiseren ons niet dat we het niet volledig hebben gewist, vooral binnen pads.
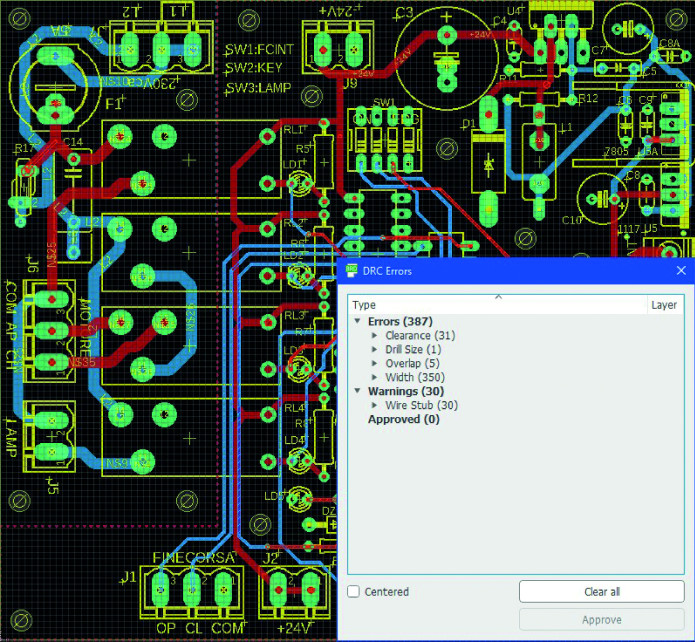
Eagle helpt ons bij het vinden en verwijderen van fouten, omdat er een markeringsvak wordt getoond dat het punt of de sectie aangeeft waarop de geselecteerde fout betrekking heeft. Zo kunnen we de fouten gemakkelijk vinden om ze te corrigeren. Figuur 6 toont precies de indicatie van een doorgangsfout - het spoor dat tussen de twee pads loopt, is te dicht bij de pads en voldoet niet aan de parameters van de DRU. Daarom moet het worden verkleind of verplaatst totdat de fout is gecorrigeerd. In sommige gevallen kun je besluiten dat de fout die wordt aangegeven door de DRU-controle niet relevant is voor het maken van je prototype, in dat geval kun je die fout selecteren en op de knop Approve klikken zodat deze uit de lijst wordt verwijderd. Gebruik deze optie alleen als je precies weet wat je doet; anders kun je problemen krijgen bij het frezen en waarschijnlijk met de werking van de schakeling nadat de componenten zijn gemonteerd.
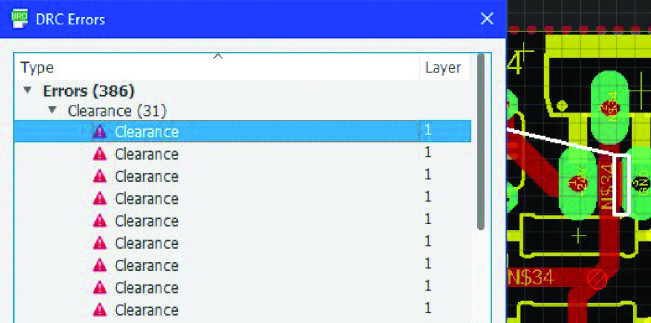
Gerber-bestand genereren
Zodra je de door de DRU aangegeven fouten hebt verwijderd (of goedgekeurd), kun je verder gaan met het maken van Gerber-bestanden, een vrij eenvoudige bewerking met Eagle.
Hieronder volgt de lijst met stappen:
- Klik op CAM Processor (figuur 7).
- · Selecteer Top Copper om de preview van de bovenkant van de PCB te controleren (handig voor dubbelzijdige SMT- of THT-prints).
- · Selecteer Bottom Copper om de preview van de bovenkant van de PCB te controleren (handig voor enkelzijdige THT print).
- · Activeer Board Shape om een rand rond de printplaat te krijgen (zal nuttig zijn bij het uiteindelijke snijden van de print).
- · Activeer Cutouts om de binnenste cirkels van de grote gaten te krijgen; klik niet op Advanced, want dat is in principe voor het spiegelen van THT PCBs. Dit doen we met FlatCAM.
- · Klik op Process Job: onmiddellijk maakt Eagle, op de geselecteerde locatie, de map CAMOutputs aan met alle bestanden die nodig zijn voor het verwerken van de print door een productiebedrijf.
Voor de volgende stappen kun je de map laten staan waar hij is gemaakt of hem verplaatsen naar een handigere locatie.
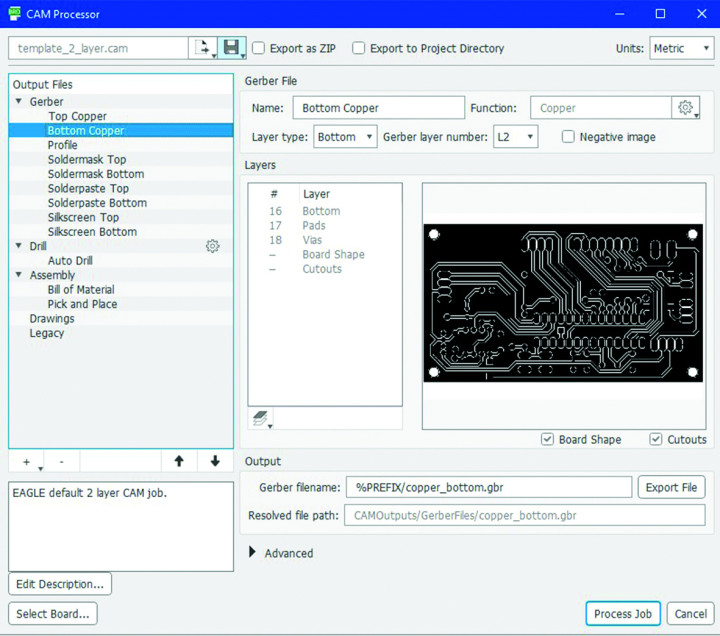
CAM-bestand genereren
Nadat je FlatCAM hebt geïnstalleerd, moet je het starten en bij gebruik voor de eerste keer moet je de volgende eenvoudige stappen uitvoeren:
- Ga naar de lege regel onderaan de programmashel (Figuur 8);
- Als de shell niet zichtbaar is, voer dan de opdrachtTool ⇒ Command line uit;
- typ get_sys excellon_zeros en druk ENTER op het toetsenbord.
- schrijf set_sys excellon_zeros T and press ENTER en druk ENTER.
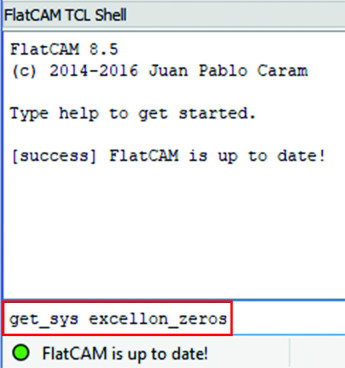
Deze twee regels code zijn nodig zodat je de gaten duidelijk kunt zien wanneer je een boortype bestand laadt; dit bespreken we later. Deze bewerking verandert de programma-opties permanent, dus het is niet de bedoeling dat dit in de toekomst nog eens herhaald moet worden. Op dit punt kun je de shell sluiten om zoveel mogelijk ruimte over te laten voor het hoofdvenster. Voer de opdracht Tool ⇒ Command line opnieuw uit.
Voer de opdracht File ⇒ Open Gerber… uit en zoek het te openen bestand in de map CAMOutputs/GerberFiles, aangezien we werken met een enkelzijdige THT print, zijn we alleen geïnteresseerd in de onderste laag (bestand copper_bottom.gbr). In het geval van SMT-schakelingen hebben we het bestand copper_top.gbr. Figuur 9 toont het type afbeelding dat je in het middelste deelvenster ziet nadat het bestand is geladen.
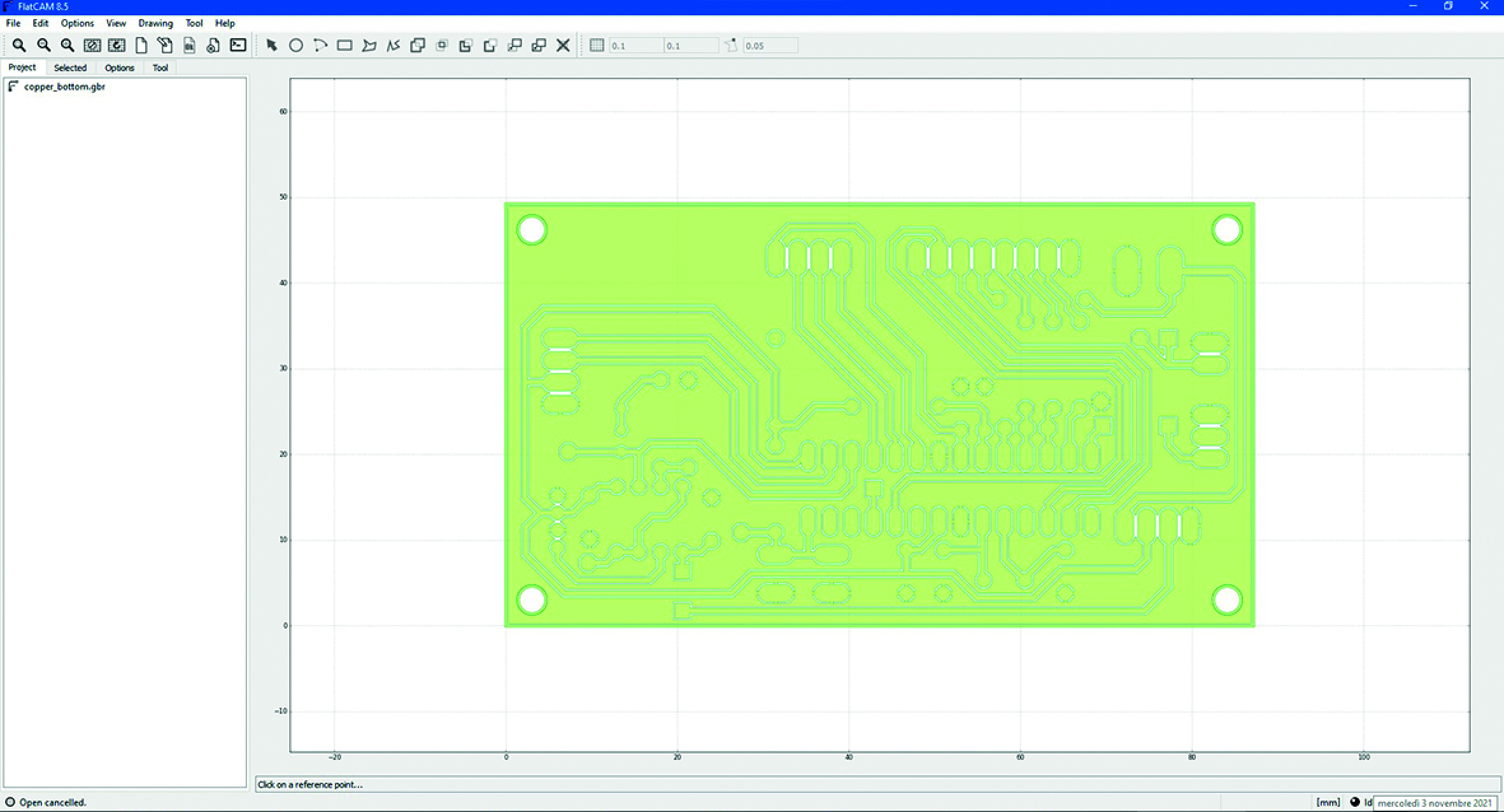
Open het tabblad Opties en schrijf in het vak Units mm. Aangezien de PCB-lay-out altijd vanaf de componentenzijde wordt gemaakt, zou het bij het frezen omgekeerd worden, dus moet er gespiegeld worden. We moeten de opdracht Tool ⇒ Double-Sided PCB Tool uitvoeren en deze parameters instellen (Figuur 10):
- Bottom layer = copper_bottom.gbr;
- Mirror axis = Y;
- Axis location = Box;
- Point/Box = copper_bottom.gbr;
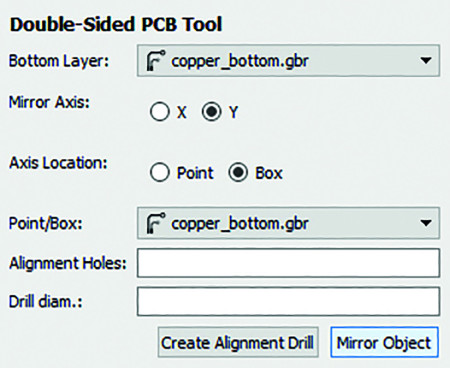
Klik op Mirror Object, de print zal nu direct zichtbaar zijn vanaf de soldeerkant (onderkant).
Let op: Natuurlijk hoeft de Tool tab niet veranderd te worden als we met de bovenkant werken (SMT-schakelingen). Open de tab Project en dubbelklik op het project copper_bottom.gbr, de tab Selected wordt geopend, en we moeten nu de volgende opties instellen
Plot opties:
- Activeer de vakjes Plot en Solid.
Isolation routing:
- Tool dia: Hier moeten we de diameter van de punt van de frees invoeren die we gaan gebruiken. De DRU die we hebben gebruikt voorziet in een afstand tussen de sporen, of tussen de sporen en het grondvlak, van 8 mils (ongeveer 0,2 mm), dus we moeten een frees kiezen met een diameter gelijk aan of een veelvoud van die waarde; we hebben 0,1 mm en 0,2 mm frezen. Als we de 0,2 mm frees gebruiken, zal de CNC in één keer precies de ruimte frezen die de DRU heeft voorzien. Als we de 0,1 mm frees gebruiken, zal de CNC-freesautomatisch twee routes naast elkaar maken om dezelfde breedte te frezen; we stellen dan 0,1 in.
-
Width: wordt gebruikt om de spoorisolatie te verhogen. Het is zinvol om dit veld te gebruiken als er geen upstream DRU wordt toegepast op de PCB. In ons geval stellen we het in op 1 (single pass). Als een groter aantal doorgangen is ingesteld, maakt de FlatCAM voor elke doorgang een grbl-bestand aan. Dan is het nodig om de print meerdere keren te frezen; bij elke nieuwe doorgang wordt de frees met een fractie verschoven die gelijk is aan de waarde die is aangegeven in het next Pass overlap-vak. Bijvoorbeeld, als de isolatie die door de DRU wordt geleverd 0,2 mm is, maar we willen het verhogen naar 0,3 mm, met een frees van 0,2 mm, vullen we in dit vak 2 in en in het volgende vak (Pass overlap) 0,5 (50%). Dan heeft de tweede doorgang 50% overlap met de eerste doorgang en er wordt dan een breedte van 0,1 mm gefreesd.
- Pass overlap: de hier aangegeven waarde wordt alleen gebruikt als Width>1; anders wordt ze genegeerd.
- Combine passes: het kan handig zijn om deze optie te activeren bij Width>1, wanneer FlatCAM een enkel bestand genereert in plaats van een aantal bestanden gelijk aan de Width waarde.
- Door op Generate Geometry te klikken, verschijnt er een rode lijn binnen de isolatiesporen, die aangeeft dat één doorgang voldoende is om het teveel aan koper te verwijderen; in figuur 11 hebben we de afbeelding vergroot en zowel het gebruik van de 0,2 mm (boven) als de 0,1 mm (onder) frees gesimuleerd om duidelijk te maken dat de CNC in het tweede geval twee doorgangen moet maken om de isolatie te produceren die de DRU verwacht.
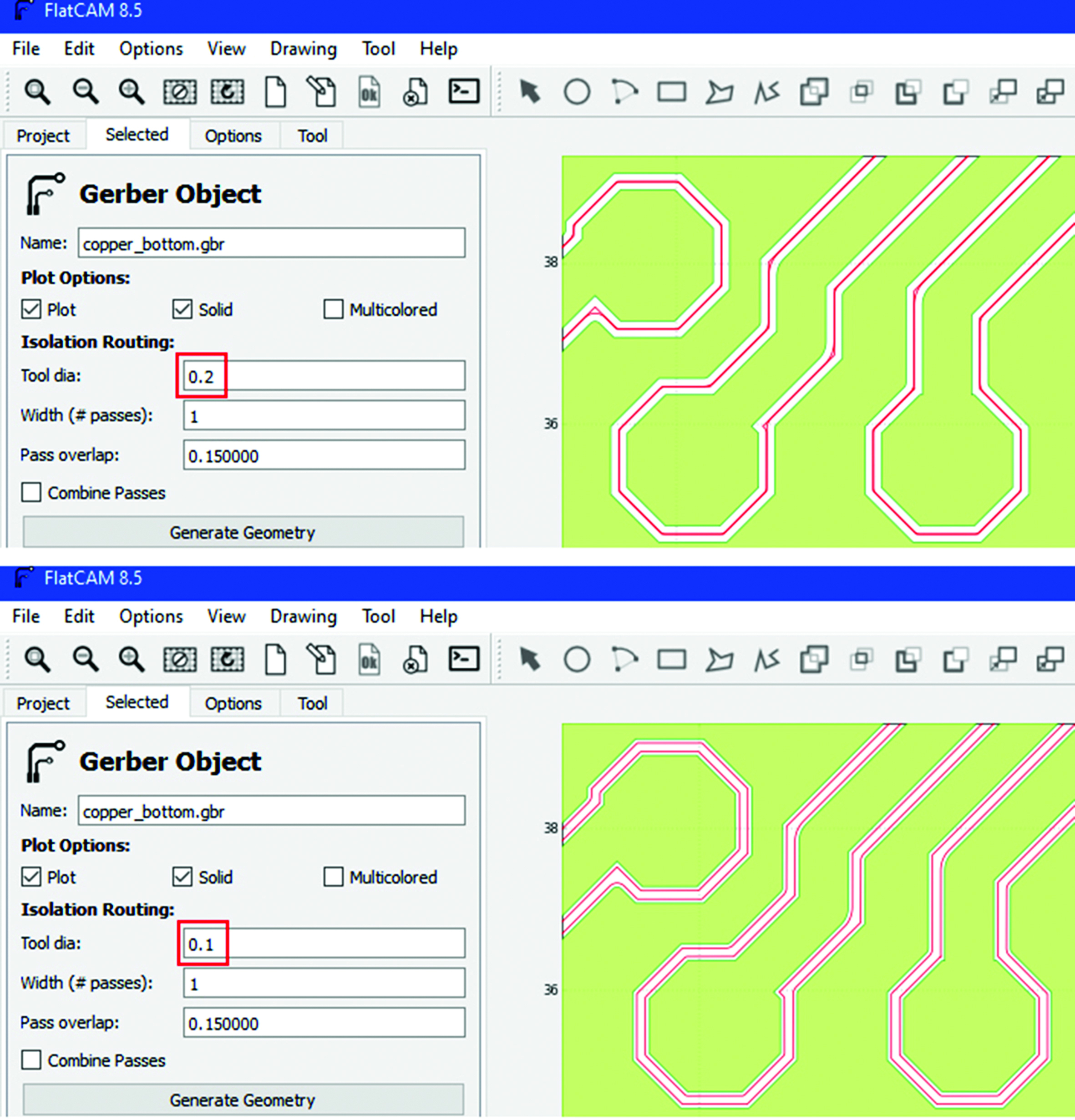
Als je na het genereren een fout ziet, moet je het volgende doen:
- Open het tabblad Project.
- Selecteer het project copper_bottom.gbr_iso dat zojuist door het programma is gemaakt.
- Druk op Delete op het toetsenbord om het te verwijderen.
- Dubbelklik op het copper_bottom.gbr project.
- Herhaal de vorige reeks taken.
Maar als alles in orde is, open dan het tabblad Project en dubbelklik op het project copper_bottom.gbr_iso. Het tabblad Selected wordt weer geopend en de volgende waarden moeten worden ingesteld:
- Plot: activeer dit vak
- Cut z: freesdiepte in millimeter; meestal is de koperdikte 0,035 mm, dus je moet een grotere waarde invoeren, ook rekening houdend met spindelbewegingstoleranties, meestal is -0,06 tot -0,08 een goede waarde.
- Travel z: is het heffen van de frees tijdens het verplaatsen, wanneer er niet gefreesd wordt. Kan op 1,5 mm worden gezet.
- Feed rate: freessnelheid in mm/min, een lage waarde duurt lang maar biedt grotere betrouwbaarheid, een hoge waarde maakt het frezen snel maar met enig risico voor de frees of verlies van stappen. We vonden een goede middenweg met een waarde tussen 50 en 80.
- Tool dia: 0,2 (dezelfde waarde als hierboven ingevoerd).
- Spindle speed: maximale rotatiesnelheid van de spindel; deze waarde is voor het verwerken van het PWM-signaal dat wordt gegenereerd door de CNC-besturing. Ons model voorziet in deze mogelijkheid en uit de datasheet van de spindel halen we dat deze bij 36 V 9000 RPM kan bereiken, dus voeren we die waarde in. Als jouw besturing een eenvoudige relaisschakeling heeft, kan dit vak leeg blijven (Figuur 12).
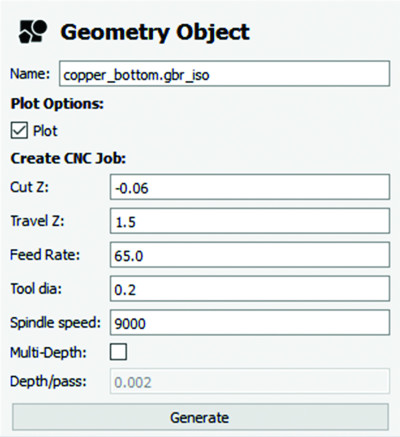
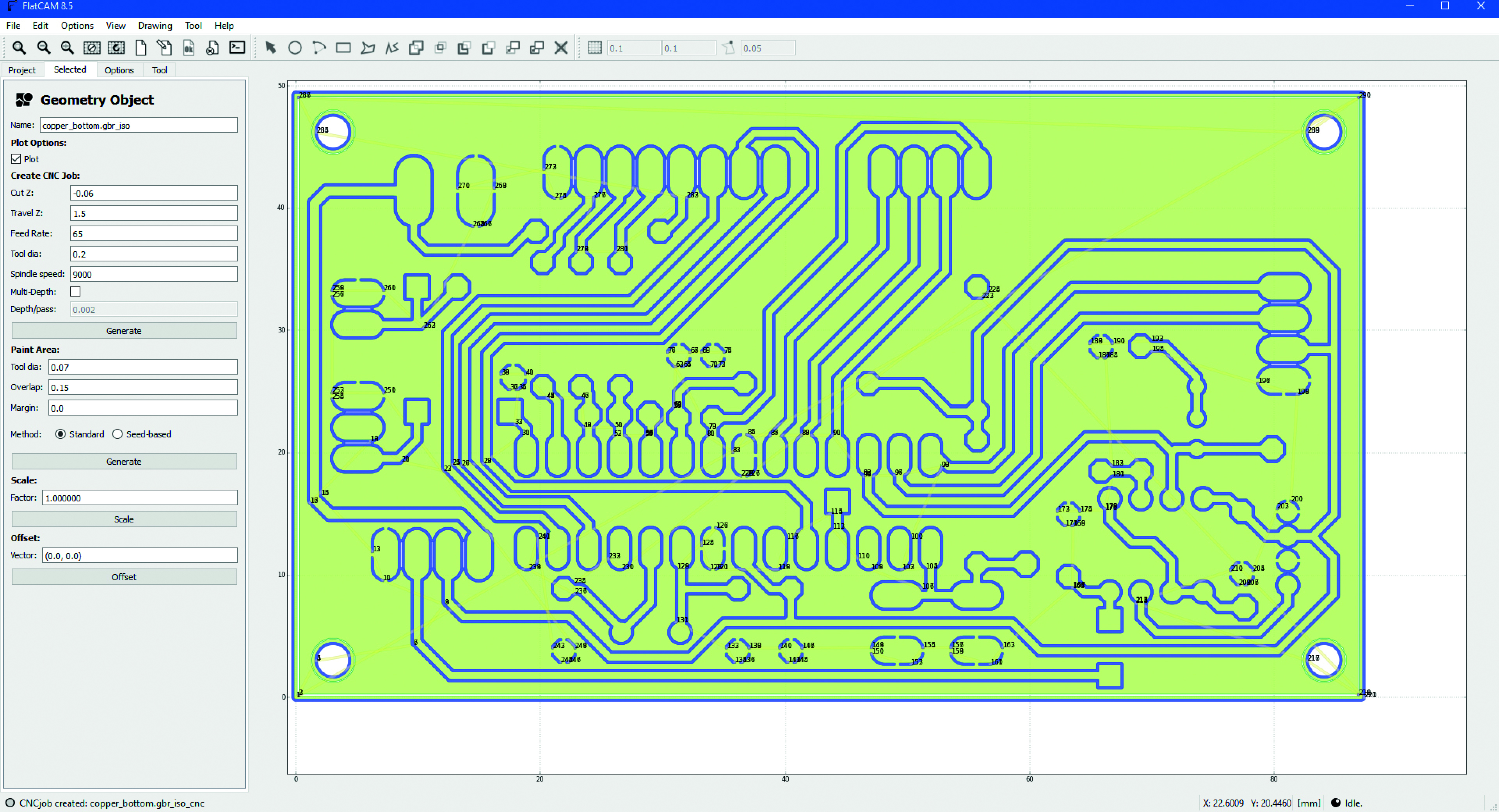
Als je na het genereren fouten ziet, moet je het volgende doen:
- Open het tabblad Project.
- Selecteer het project copper_bottom.gbr_iso_cnc dat zojuist door het programma is gemaakt.
- Druk Delete op het toetsenbord om het te verwijderen.
- Dubbelklik op het projectcopper_bottom.gbr_iso;
- Herhaal de vorige reeks taken.
Als daarentegen alles oké is, open dan het tabblad Project en dubbelklik op het project copper_bottom.gbr_iso_cnc, en het tabblad Selected gaat weer open. Vervolgens activeren we de optie Plot en voeren we in het veld Tool dia dezelfde waarde in als voorheen (in ons geval 0.2). Klik dan op Update Plot, wacht een paar seconden, er gebeurt ogenschijnlijk niets, en klik dan op Export G-Code en sla het bestand op als Name_PCB.nc, waarbij Name de naam van je project is. Het is niet verplicht om een specifieke naam aan te geven, maar als je dat wel doet, kun je een map maken met al je bestanden, voor toekomstig gebruik. Het enige wat essentieel is, is de extensie .nc, anders wordt het bestand niet gezien door de Candle software.
Als je ontwerp SMD-componenten bevat en er dus geen gaten nodig zijn, kun je FlatCAM sluiten en direct naar de freesfase gaan. Anders moet je doorgaan met de volgende stap van dit programma.
CAM-gatenbestand genereren
Voer de opdracht File ⇒ Open Excellon… uit en open het bestand drill_1_16.xln, fdat zich in de map CAMOutputs/DrillFiles. Als je de print eerder hebt gespiegeld, zul je zien dat de gaten (weergegeven door rode cirkels) niet overeenkomen met de onderliggende pads of vias (Figuur 14); Je moet het commando Tool ⇒ Double-Sided PCB Tool uitvoeren en deze parameters instellen:
- Bottom layer = drill_1_16.xln;
- Mirror axis = Y;
- Axis location = Box;
- Point/Box = copper_bottom.gbr.
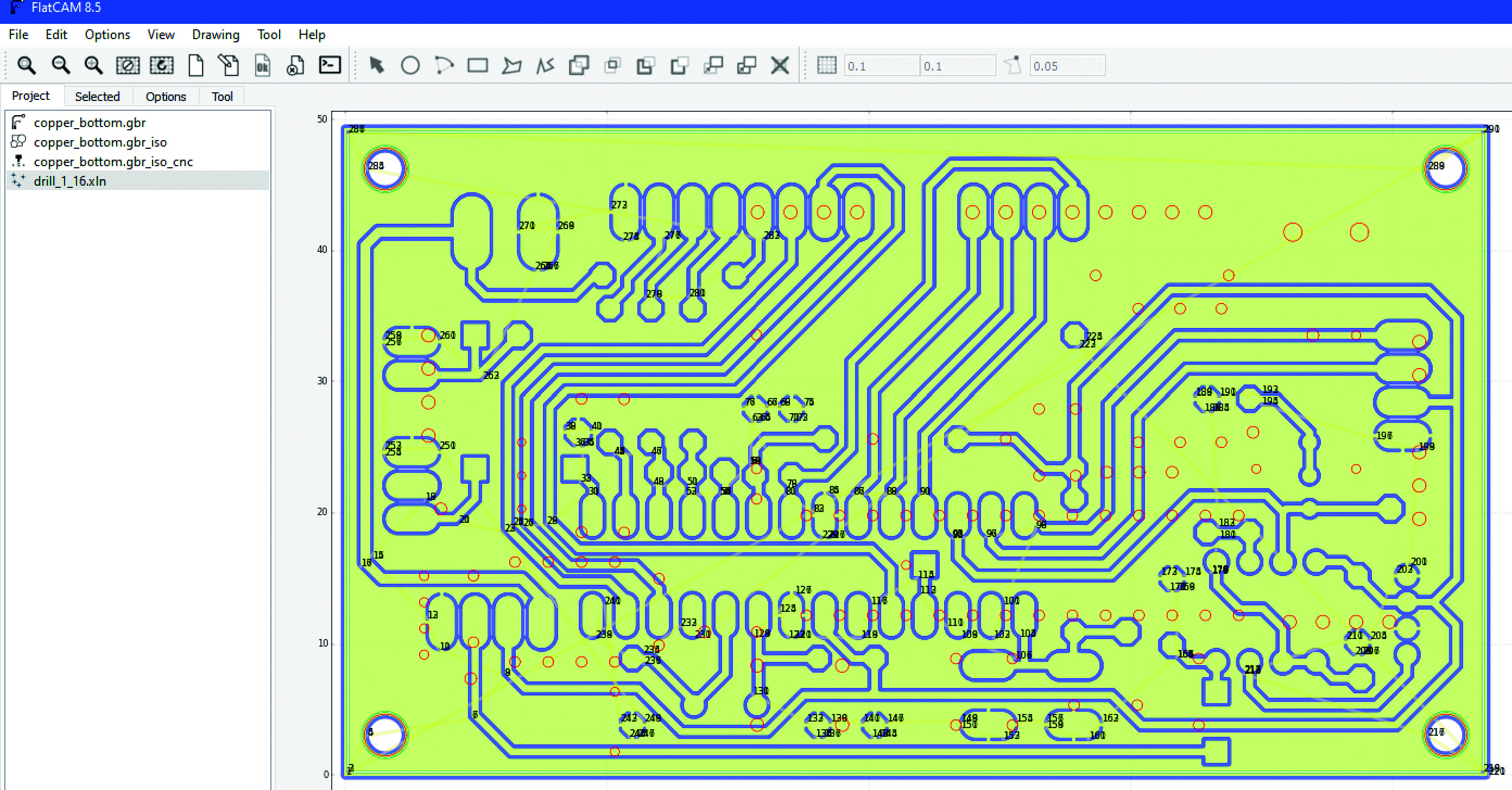
Klik op Mirror Object en de gaten zullen onmiddellijk perfect gecentreerd zijn ten opzichte van de onderliggende pads en vias (Figuur 15). Als je fouten bemerkt na het spiegelen, moet je de volgende stappen uitvoeren:
- Open het tabblad Project;
- Verwijder het project drill_1_16.xln door Delete te drukken op het toetsenbord;
- Voer de opdracht File ⇒ Open Excellon… uit en open het bestand drill_1_16.xln
- Herhaal de vorige reeks handelingen.
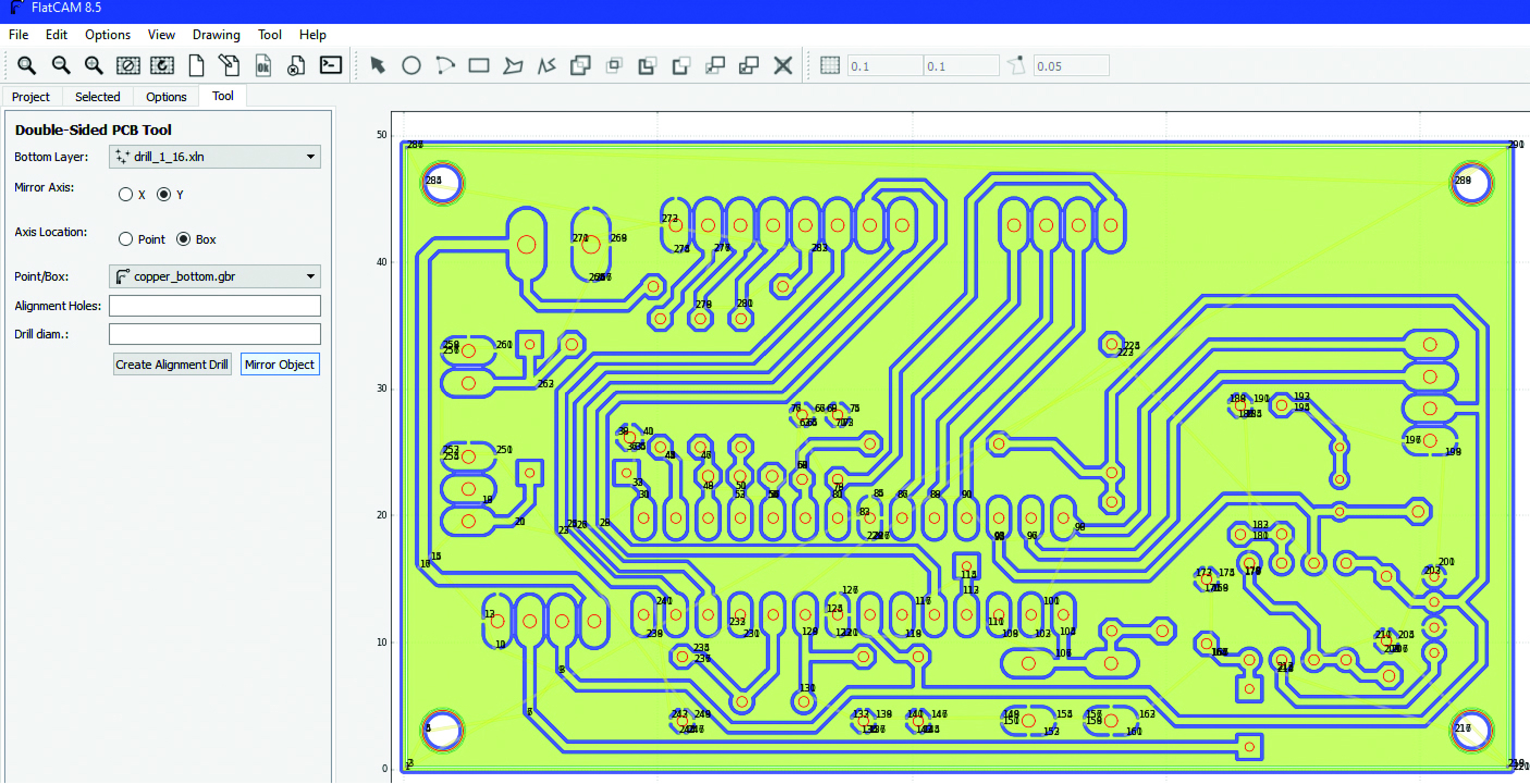
Als alles in orde is, open je het tabblad Project en dubbelklik je op het project drill_1_16.xln. Het tabblad Selected wordt opnieuw geopend en je moet de volgende waarden instellen:
Plot opties
- Plot: activeer het vak;
Gereedschap
- Tools: controleer de volgorde van de diameters, deze moet oplopend zijn, anders klik je op #. Deze waarden zijn de diameters van de boren die nodig zullen zijn om de printplaat te boren. Zoals je zult merken, zijn sommige waarden niet standaard, maar de afwijkingen zijn tienden of honderdsten van een millimeter. Het enige wat je moet doen is ze virtueel afronden en dan de boren met de dichtstbijzijnde waarde gebruiken, op het moment dat ze nodig zijn.
Bijvoorbeeld: voor 0,61 gebruik je een 0,6 mm boortje, voor 0,686 en 0,7 gebruik je altijd de 0,7 mm boor.
CNC taak maken
- Cut z: diepte van het boorgat. Een PCB is meestal 1,6 mm dik, dus de in te voeren waarde is dan meestal -2,5, als de PCB bevestigd wordt op de steunen die boven de plaat uitsteken, zoals in ons geval. Selecteer alle gereedschap-ID's met de muis, wat cruciaal is voor het genereren van het grbl-bestand.
- Travel z: mm boorheffing om naar de volgende boring te gaan. Kies hier 1,5.
- Feed rate: snelheid van de Z-as tijdens het boren, in eenheden per minuut; het programma beveelt een waarde van 3,0 aan, maar voor ons doel kun je beter een waarde van 30 tot 50 kiezen;
- Tool change: activeer het vakje zodat de CNC stopt als het gereedschap uitgewisseld moet worden;
- Tool change z: 30 (mm of spindle lift to allow bit change)
- Spindle speed: spindelrotatiesnelheid, hetzelfde als hierboven uitgelegd is van toepassing, dus voor onze CNC-machine stellen we 9000 in, maar als je een ander model spindel hebt, moet je de datasheet raadplegen.
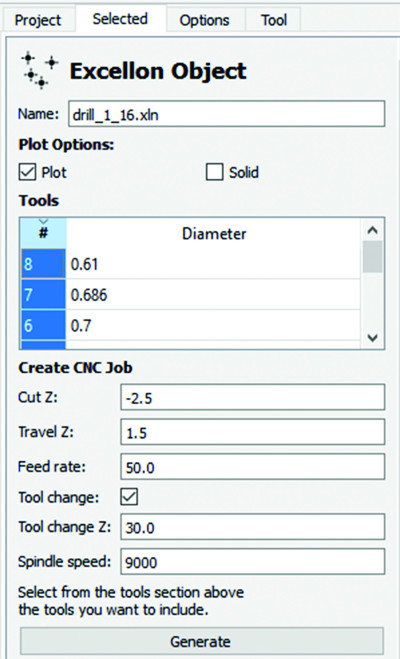
In Figuur 16 hebben we de zojuist beschreven sectie weergegeven met de ingestelde waarden.
Klik op Generate en alle gaten worden genummerd volgens de boorvolgorde (figuur 17); als dit niet gebeurt, helemaal niet of alleen bij sommige gaten, dan betekent dit dat de gereedschaps-ID's niet juist zijn geselecteerd. Als je een fout bemerkt na het uitvoeren van deze laatste bewerking, moet je deze stappen uitvoeren:
- Open het tabblad Project.
- Selecteer het project drill_1_16.xln_cnc dat zojuist door het programma is gemaakt.
- Druk op Delete op het toetsenbord om het te verwijderen.
- Herhaal de vorige reeks stappen.
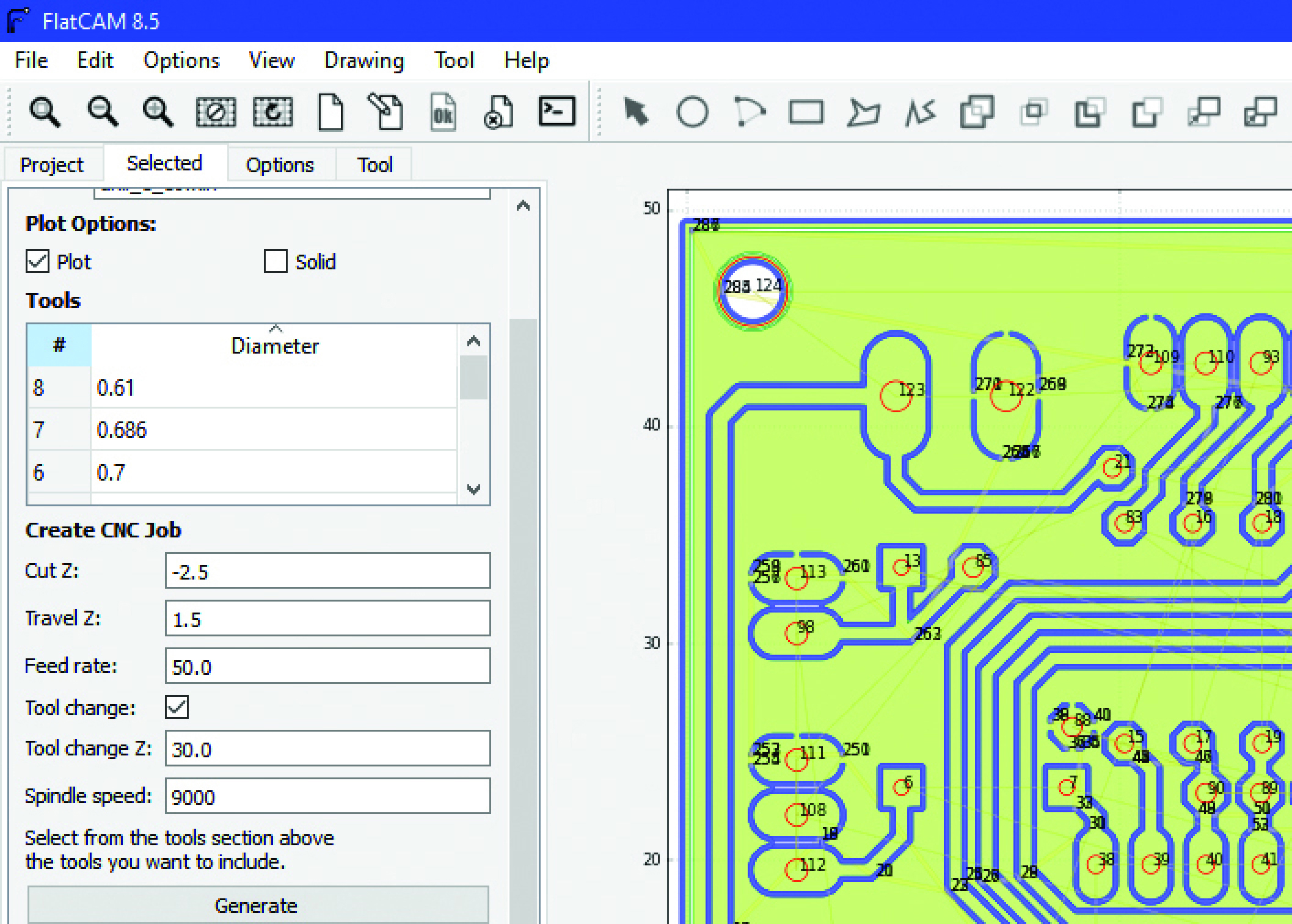
Als alles in orde is, open je het tabblad Project en dubbelklik je op het project drill_1_16.xln_cnc. Het tabblad Selected wordt opnieuw geopend en je moet de volgende waarde instellen:
- Tool dia: 0,6 (standaard initiële boordiameter).
- Klik op Update Plot. De afbeelding toont nu ook het boorpad (figuur 18).
- Klik op Export G-Code.
- Sla op met Name_FORI.nc, waarbij Name de naam van je project is, zoals eerder gezegd voor het trackbestand; ook hier is het essentieel om de extensie .nc te gebruiken, anders wordt het bestand niet herkend door de Candle software.
Met deze laatste stap hebben we de CAM-bewerkingen afgerond en hebben we nu twee bestanden in grbl-formaat, waarmee we het printmateriaal gaan bewerken. Eerst verwijderen we het overtollige koper en daarna boren we de benodigde gaten voor de componenten.
Let op: Het is belangrijk om het FlatCAM project op te slaan, eventueel in dezelfde map als de grbl bestanden, zodat je het opnieuw kunt openen om snel een parameter te wijzigen, zonder alle stappen tot nu toe opnieuw te moeten doen. Het commando dat je moet gebruiken is File ⇒ Save Project As..., waarbij je het pad en de naam opgeeft (meestal dezelfde als die van de twee grbl-bestanden), zoals Name_prj zonder extensie, waarbij Name altijd de naam is die eerder is gebruikt. In de volgende aflevering gaan we verder met het praktische gedeelte, met een diepgaande studie van het Candle programma en het maken van onze eerste print.

Discussie (3 opmerking(en))
Wil Schreuders 1 jaar geleden
Henk Waaijer 1 jaar geleden
acveldis 1 jaar geleden