A simulator for Hardware-in-the-loop control system validation
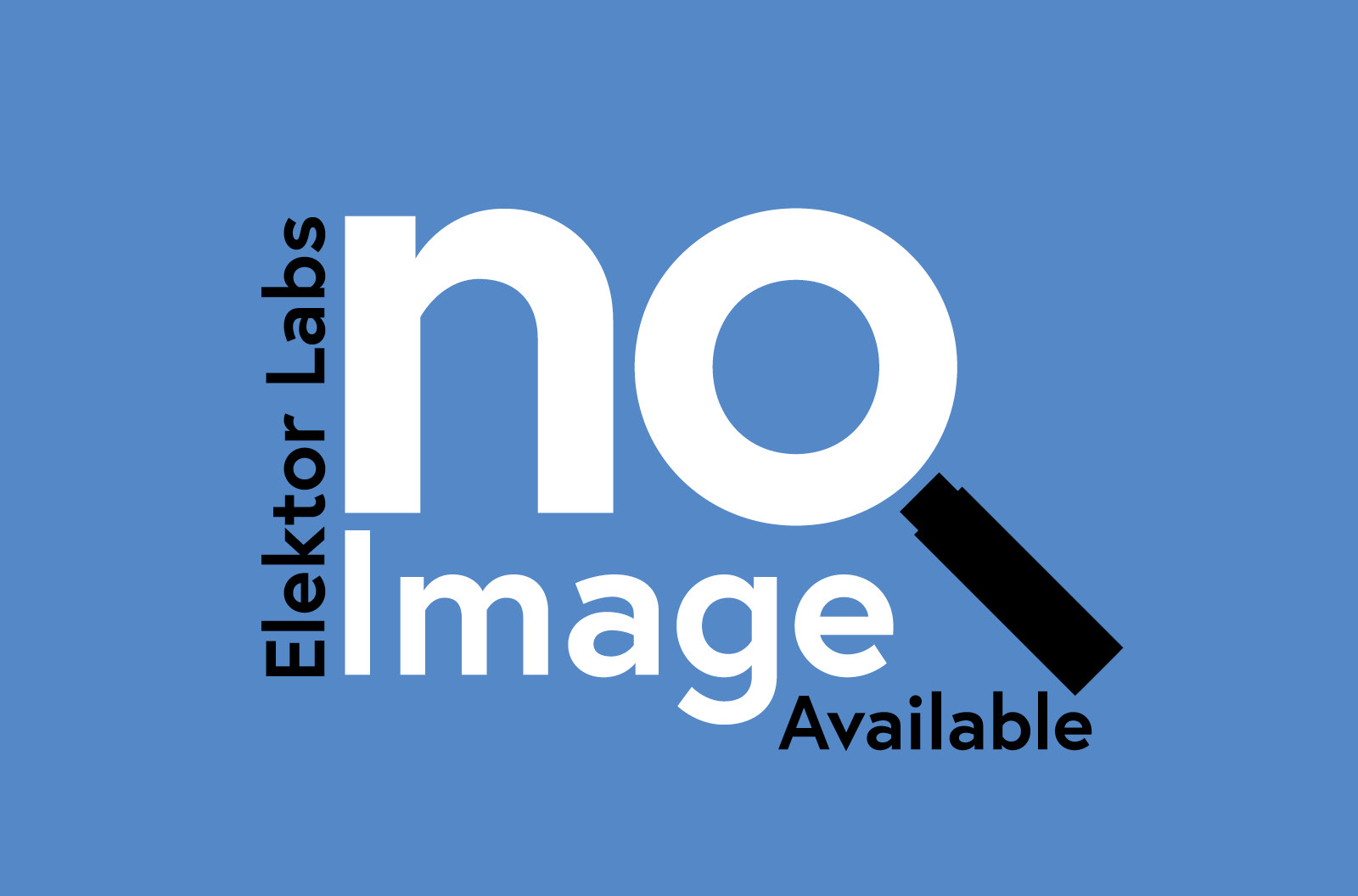
During control system evaluation it is cumbersome, costly or dangerous to use the real plant in the tests. A method to simulate the plant using Neural Networks is proposed.
An important part of control system development is testing and validation.
In general, much of this testing is carried out with various system components simulated in software. One common scenario is hardware-in-the-loop.
In this testing scenario, the control function is performed by the actual control hardware, that can be a custom control system, a commercial Distributed Control System (or DCS) or the control part of an apparatus or vehicle.
This real-time control hardware that in actual use is connected to the controlled plant, is connected instead to a model of that plant. This model receives the control outputs from the control system under test and as a response, outputs the measured variables that are connected to the control system's sensor inputs.
The model is capable of receiving and transmitting those variables in a format compatible with the
controller's interface circuits.
These measurements are often conveyed as industry standard signal types, for example 1-5 V or 4-20 mA, or by some kind of industrial field bus.. For analog signals, the ADC inputs can be used or in the case of the MAX78000FTHR where not all the pins are exposed an ADC to I2C converter like the MAX11608 can be used. The part has no analog output so in case they are needed a digital to analog converter with I2C interface like tjhe MAX5816 can be used,
The difference from usual implementation is the ability of Convolutional Neural Networks to model arbitrary non llinear functions. Most hardware-in.the-loop models are often simplified as linear representations that can be represented by simple equations: some responses like inverse first response are difficult to model. As this is not a familiar method in control systems implementation, the design and training of the network representation will be the next challenge.
Unfortunately the kit arrived a few days ago and I was not able to make any progress with the implementation.
In general, much of this testing is carried out with various system components simulated in software. One common scenario is hardware-in-the-loop.
In this testing scenario, the control function is performed by the actual control hardware, that can be a custom control system, a commercial Distributed Control System (or DCS) or the control part of an apparatus or vehicle.
This real-time control hardware that in actual use is connected to the controlled plant, is connected instead to a model of that plant. This model receives the control outputs from the control system under test and as a response, outputs the measured variables that are connected to the control system's sensor inputs.
The model is capable of receiving and transmitting those variables in a format compatible with the
controller's interface circuits.
These measurements are often conveyed as industry standard signal types, for example 1-5 V or 4-20 mA, or by some kind of industrial field bus.. For analog signals, the ADC inputs can be used or in the case of the MAX78000FTHR where not all the pins are exposed an ADC to I2C converter like the MAX11608 can be used. The part has no analog output so in case they are needed a digital to analog converter with I2C interface like tjhe MAX5816 can be used,
The difference from usual implementation is the ability of Convolutional Neural Networks to model arbitrary non llinear functions. Most hardware-in.the-loop models are often simplified as linear representations that can be represented by simple equations: some responses like inverse first response are difficult to model. As this is not a familiar method in control systems implementation, the design and training of the network representation will be the next challenge.
Unfortunately the kit arrived a few days ago and I was not able to make any progress with the implementation.
Discussie (0 opmerking(en))