CO2 Guard [210043]

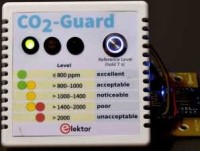
CO2 400-2000 ppm, 3 LED's , level/temp sensor logged to ThingSpeak, buzzer, ESP8266
Designed by Florian Schäffer
This CO2 Guard is used for indoor air monitoring and assessment of the air quality (IAQ: Indoor Air Quality) based on the carbon dioxide concentration. A CO2 concentration in the interior of less than 1000 ppm (0.1 vol%) indicates a hygienically adequate air exchange under normal conditions and can help to minimize the risk of infection with COVID-19.
About the circuit
Heart of the circuit is a Wemos D1 mini, a small Wi-Fi board with 4MB flash based on ESP-8266EX. It’s used to get data from the sensor MH-Z19C by I2C, drive three LED's for indication of the CO2 levels, drive a buzzer to serve as an acoustic alarm when levels are unacceptable, supply 3.3 V for a miniature fan, supply 5 V for the sensor and an extra led inside a switch to indicate a W-Fi connection is active. The micro-USB connector serves as power supply. A 5VDC AC adapter with micro-USB connector is needed as a power supply for the CO2-Guard. The switch is connected to the sensor to perform a calibration. According to the datasheet the sensor must be active in an environment with 400 ppm CO2 level for more than 20 minutes before the HD input is pulled low for over seven seconds by S1. The manufacturer calls it zero point calibration, but we prefer the term reference level since calibration is done at 400 ppm. If not performed by hand calibration is done automatically every 24 hours if continuously powered by taking the lowest level measured as reference level. Outside the air is about 400 ppm and this CO2-Guard is meant for rooms that aren’t used by people full time, let’s say only during normal working hours.
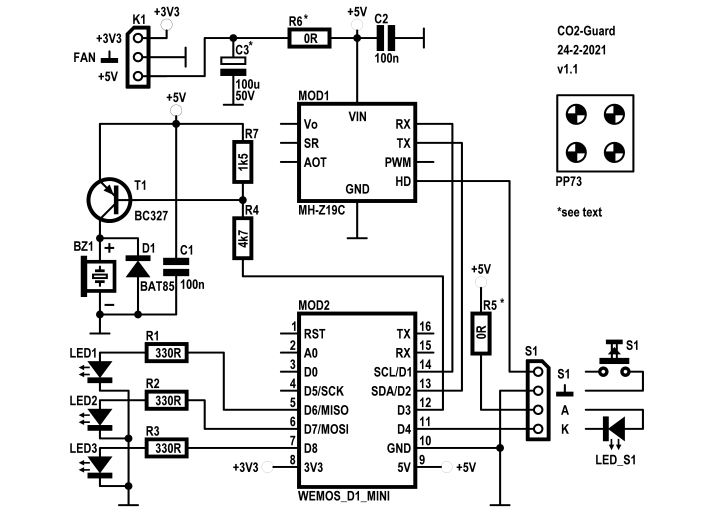
The 5 V fan is connected to the 3.3 V output of the D1 mini via connector K1, to make it run more silent and cause less airflow. Feel free to solder the wires directly into the PCB if so desired. Dust build-up will be less with less airflow. The 3.3 V on the module is created by a ME6211 regulator in a SOT23-5 package. Maximum dissipation of the regulator is 250 mW and this will limit the maximum current of the 3.3 V output of the D1 mini to less than 150 mA. It's. not advisable to use this (theoretical) maximum output current. It’s not specified by the manufacturer of the board(?). To avoid this “heavy” load on the 3.3 V regulator there’s an option on the PCB of the CO2-Guard to connect the fan through a resistor (R6, footprint for 1 W type) directly to the 5 V. This makes it possible to reduce the airflow even further. But, a too high resistor value and the fan won’t start at power-up. A capacitor (C3, 100µF) across the fan can lower this voltage level but should be tested before mounting the final R6 and C3. It depends on the fan used, even a fan from the same series can give a different maximum value for R6. It also depends on temperature rise of the fan! If the fan is to be connected to the 5 V directly a wire jumper wire can be used for R6 instead.
The buzzer also uses the 5 V supply. The output level of the I/O’s of the D1 mini when high is 3.3 V. To turn the buzzer off voltage divider R4/R7 is connected to the base of PNP transistor T1. Some buzzers are inductive and likely to produce spikes, especially when turned off. Diode D1 prevent these spikes from harming the transistor. De buzzer has a footprint with a pitch of 5 and 7.62 mm, so there’s also a pitch of 6.31 mm where a buzzer with 6.5 lead spacing should fit.
The switch (momentary on) we used is one with an optical indicator in the form of a blue ring. No resistor is needed for the led in the switch. + and – next to two pins of the switch indicate the two connections of the LED. The other two pins are connected to the switch. Four wires (three with common ground for led and switch) are connected to a 4-way pin header (or solder the wires directly to the PCB). If the circuit is used in a different setting a separate switch and LED can also be used. R5 sets the current for the separate LED. Here R5 is not needed and a jumper wire should be used in it’s place on the PCB (next to D1).
Make sure no wires lie on the antenna when the top is finally placed on the bottom part of the enclosure. Keep them as far away as possible but don’t make them longer than absolutely necessary. Wires to the switch can be as short as 8,5 cm and the wires to the LED's about 12 cm. With this length of the wires you can remove the top of the enclosure and place it on its side next to the bottom with all wires still attached. No screws are used to attached the two parts of the enclosure. 4 long plastic pins of the top slide in to 4 long mounting bosses.
Preparing the enclosure
Use the front layout (see Project Elements for zipped BMP file) as a template for the correct position of the 4 holes, little marks are added in the center of the circles on the sticker. Be very careful when drilling in plastic enclosures. If drilling is done too fast or at first a too large drill size is used, the drill can “bite” and instead of a nice round hole there’s an ugly gap in it. So, to avoid this from happening mount the top side of the enclosure in a drill press vice and use a drill press (don't drill out of hand). First drill with a smaller drill then needed, e.g. 2.5 mm for the LED’s and slowly increase drill size for the correct size for the LED housings. Drilling 12 mm inside plastic takes experience, if done move the drill slowly in small steps up and down and remove chips regularly (the little strips of plastic that come of the drill). Give the chips a chance to clear the hole, but never touch the drill when it’s rotating!!! If the chips are not removed while drilling, these pieces can make the drill easily “bite” because the plastic is soft. The hole for the switch can be made by using a smaller drill, for instance 9 or 10 mm, first and then use a half-round file to increase the hole size to perfectly fit the switch. Drilling with 12 mm in soft plastic takes experience and if the drill bytes the rather large gap in the edge of the hole can be the result. Or, mark the 12 mm circle for the switch on the enclosure and use a small drill to make a kind of perforation inside the circle. Push out the center and file the rough edge to the 12 mm marked circle. Be careful, it’s plastic and filing takes little effort, not to say can be too easy. So always check size and position regularly, take your time and use little force then. When handling the top halve take good care not breaking the four plastic pins that secure the top halve in the bottom halve, no screws are used to hold them together. When drilling in the top place a piece of wood that will fit inside the top to prevent it from bending when pushing the drill through it.
USB connection
A notch must be made in one side of the bottom half of the enclosure to connect a 5 V USB DC adapter to the D1 mini module, which serves as the power supply for the CO2-Guard. For an an ordinary connector to fit the notch must be big enough to fit the full size of the connector, otherwise the connector can't be pushed through far enough. There are cables with an extended/longer metal part of the USB connector, then the notch can be made smaller. Place the D1 mini module on the PCB to mark the correct place for the notch. No need to solder the module with the accompanying male headers to the PCB yet. With the module placed on the PCB and the PCB placed correctly on the screw fixings, maybe use 2 screws temporarily, the position of the notch can be marked, it’s slightly of center.
Fan
No holes have to be made for the fan, it’s glued to the bottom side using super glue or epoxy adhesive. To avoid resonance the fan should not touch the top half of the enclosure. The fan should blow air out of the enclosure, before mounting it check the direction of the airflow by connecting it to a 3.3…5 V power supply. Pay close attention to polarity, wrong polarity may or will damage the fan (modern ones often have a small circuit inside). There’s probably a small header connected to the wires of the fan. Remove it (simply cut it and strip the ends of the two wires). The wires of the fan can be shortened since the connector on the PCB is right next to it. Preferably solder the wires directly to the header on the PCB (a socket can of coarse also be used, but there’ always a chance it will get loose over time).
LEDs
To connect the LED's only four wires are needed. Ground connection from the PCB to three LED's on the front can be one common connection. Connect the three cathodes of the LED's to use a single wire. Only a 5-pin header is needed on the PCB then.
PCB
All parts are through hole and the PCB is single sided, which makes removing parts relatively easy. A simple manual desoldering pump works fine if ever needed, since there are no metalized holes. But the number of parts is low and a mistake is not likely. Start mounting the lowest parts first. Start with the resistors and then diode, capacitors, transistor, buzzer and headers (sockets for the sensor MOD1, male headers for the switch, LED's and fan). Before you do this you can mount the D1 mini module (after programming it) but not MOD1 yet (the sensor module itself). To mount the D1 mini module (MOD2) first solder the two 8-pin male headers to the side of the module where the USB connector is located (see photo's below). We advise not use sockets on the PCB for MOD2 here. Since there’s some force on the module when plugging and unplugging the USB connector it’s best to solder the D1 mini onto the PCB. Also, on sockets it will limit airflow through the ventilation holes of the enclosure somewhat.
When the PCB is fixed with four screws to the bottom half of the enclosure and the fan glued the sensor module can be attached to the corresponding sockets.Never touch the top of the sensor, from the datasheet: Please avoid the pressure of its gilded plastic chamber from any direction, during welding, installation, and use. Especially never touch the air intake (white dust filter).
The 4-pin and 5 pin socket for the sensor probably come as one 10-pin SIL socket. Cut the 5th pin in half to get a separate 4 and 5-pin pin socket. Trying to break them usually happens in the middle of a pin anyway.
Also, a single 12-pin male SIL header must be separated into a 3-, 4- and 5-pin header for the fan switch/LED and the three LED’s.
Of coarse feel free to create your own front design. You can use a separate blue LED and switch for instance. But be aware of placement of the LED’s and switch, so they don’t come to close to the modules. Size of the area on the enclosure is 70.2 mm square.
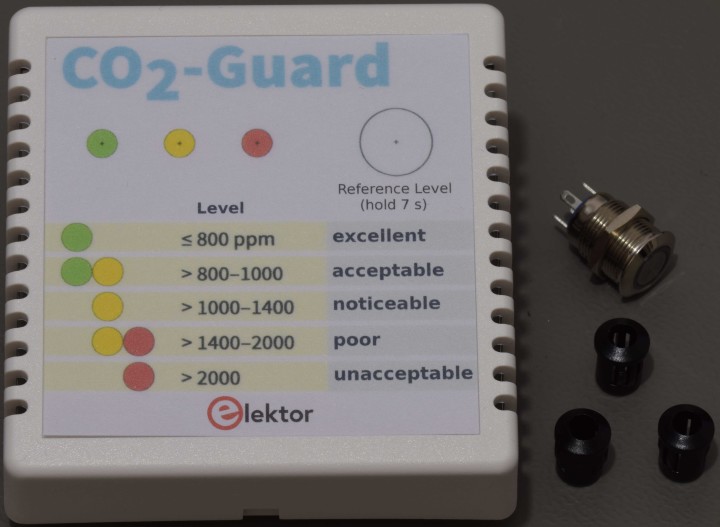
Photos: getting PCB and enclosure ready Top half of enclosure with paper copy of sticker on it to mark the place for the holes, led housings and switch next to it.
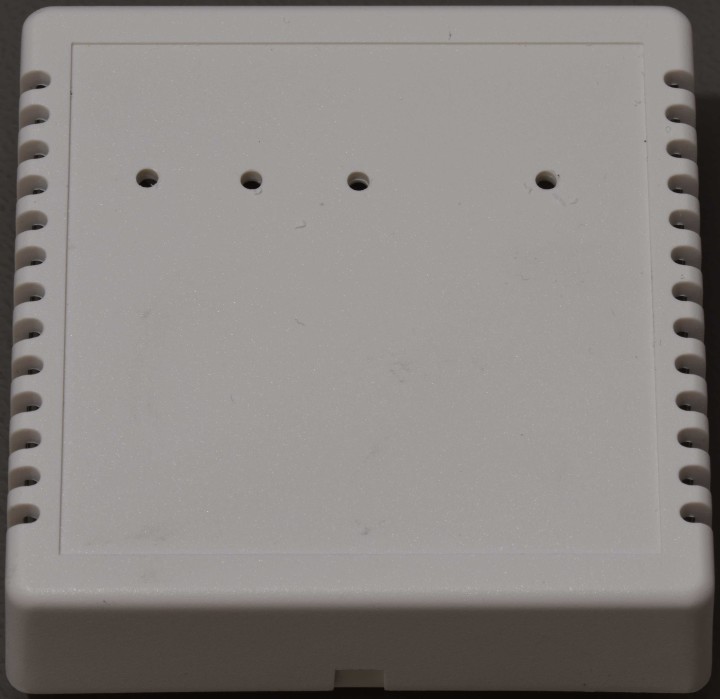
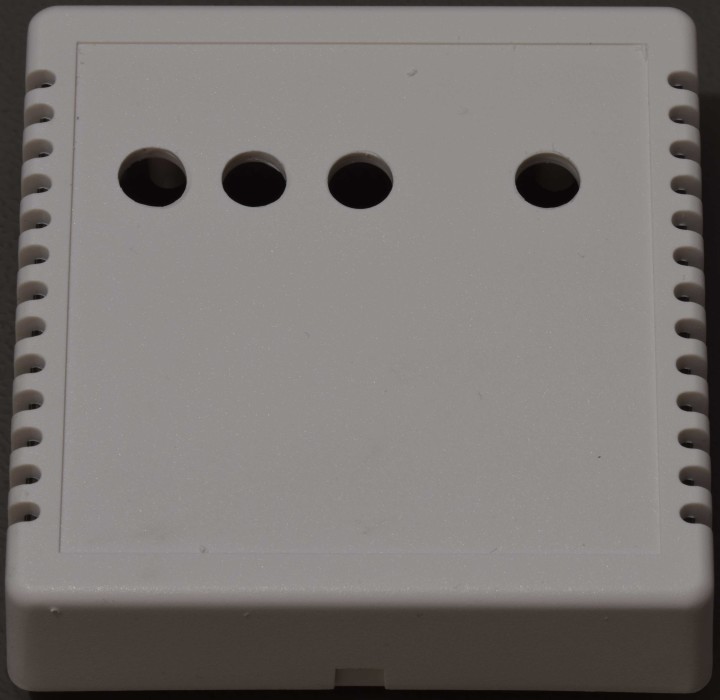
4 holes with 8 mm drill. The three holes for the led housings are finished.
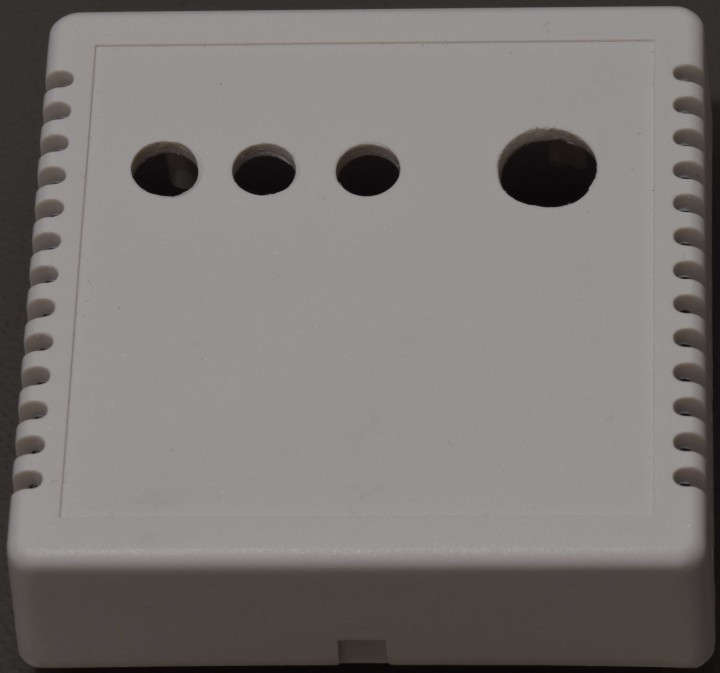
The hole of the switch is enlarged to the correct diameter using a round file. Took about a minute, so be careful not to file too much!
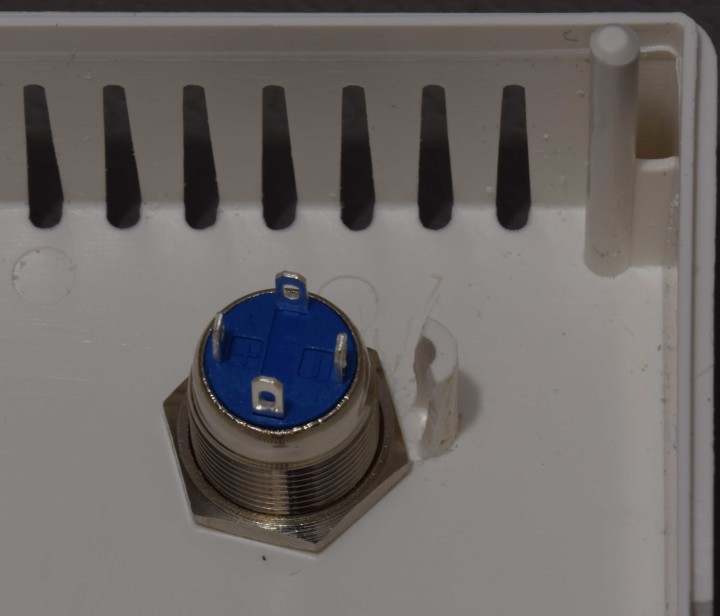
Removed part of a stand-off on the top half of the enclosure so the nut of the switch can be placed to secure the switch to the front.
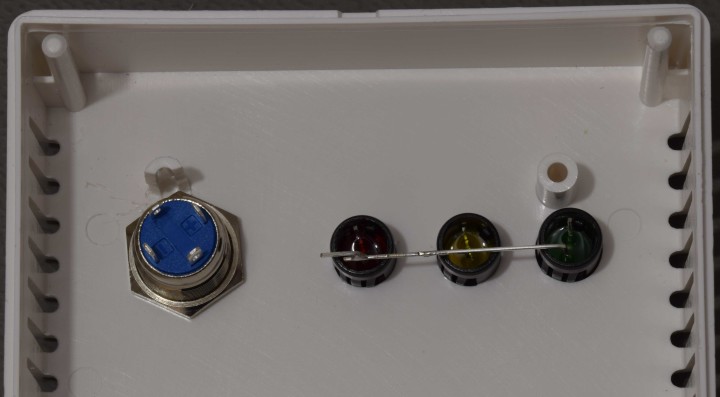
LED housings with LED's and switch mounted.
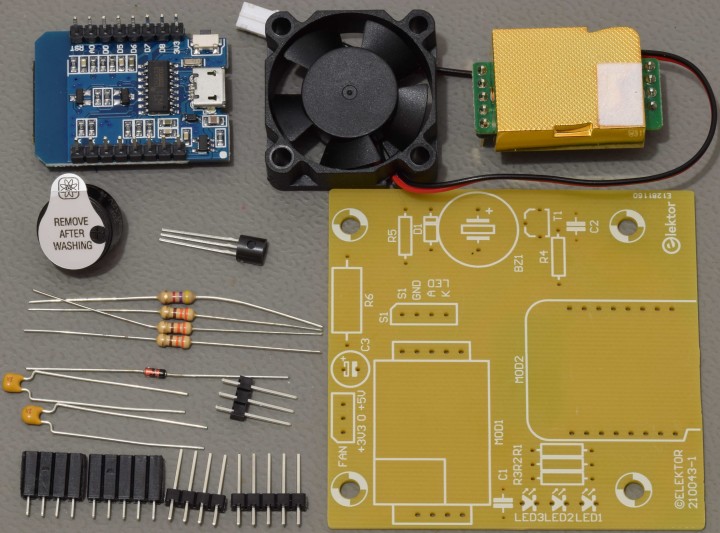
Overview of PCB, all parts of our prototype that are to be placed on it and the fan.
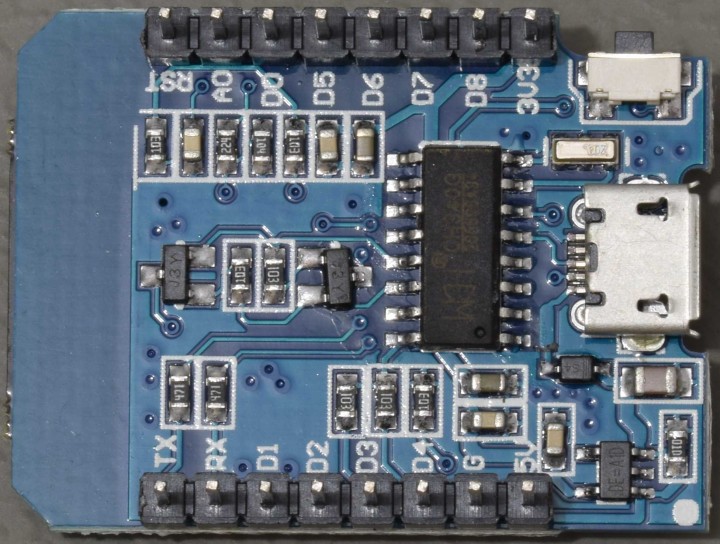
Solder the two 8-pin male headers to the D1 mini module
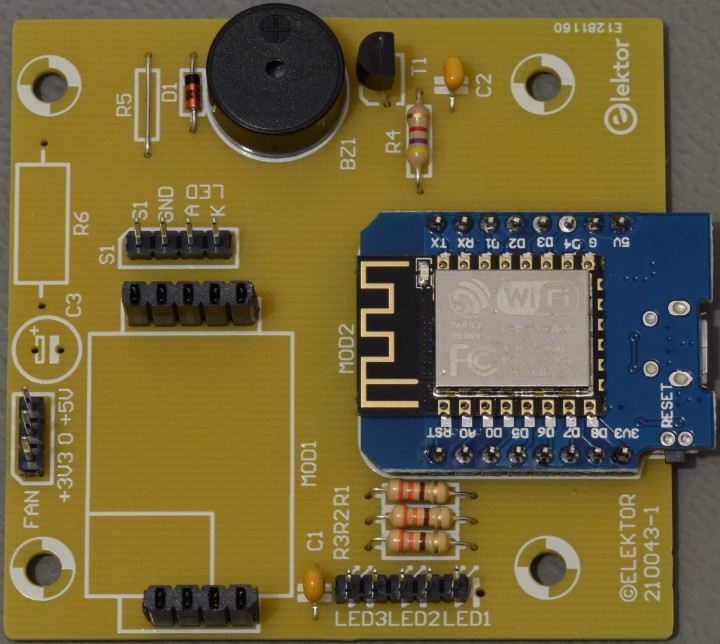
Solder the D1 mini module to the PCB after all other components are mounted.
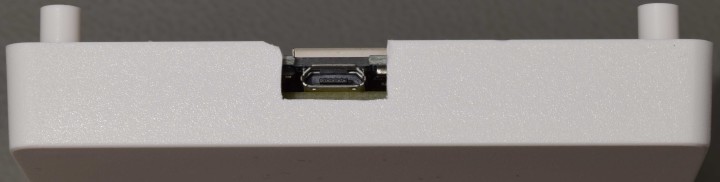
Opening for a standard size micro-USB connector, view from the side. A small sharp knife was used. Don’t use too much force or the knife may slip and cut too much. A tiny bit of one side was chipped off. And always cut away from your fingers!!!
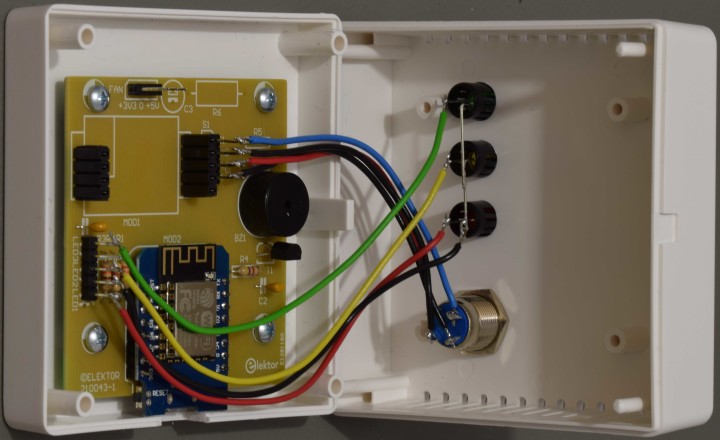
Place the top of the enclosure as close as possible to the bottom part. Connect LED's and the switch. Keep cable length to an absolute minimum. Here the 4 wires for the LED's are 12 cm long, the wires for the switch are 8.5 cm long. In a final version consider using heat shrink tubes to insulate the solder joints. Make sure when the enclosure is closed no wires are interfering with the antenna on the D1 mini module!

The fan can be glued to the bottom before putting the top on the enclosure. Don't forget to solder the wires of the fan to the connector next to it. Place the CO2 sensor. Do not put pressure on the gilded plastic chamber! Hold the sensor at the edges where the pins are to press the sensor into the sockets on the PCB.
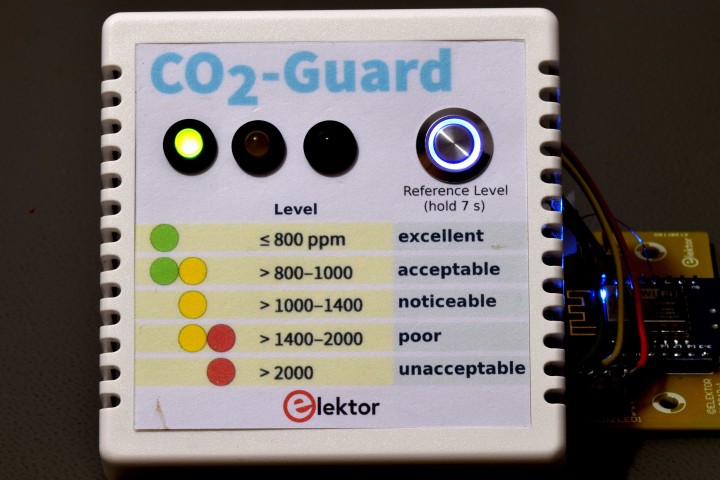
Testing WiFi. When connected to your router the blue led of the switch should light.
Install Arduino IDE (do this before mounting the D1 mini on the PCB)
Download from here: https://www.arduino.cc/en/software, and save the file to a preferred location on your computer. Double click on the executable file and follow the instructions. Always click on ‘Install’ if asked for installing device software. Click on ‘Close’ when ‘Arduino Setup: Completed’ appears.
The D1 mini module uses a USB controller chip (CH340) which is not automatically recognized by Windows 10. If the CH340 IC is not recognized download the driver from the manufacturers website, here: http://www.wch-ic.com/downloads/CH341SER_EXE.html and download the file CH341SER.ZIP for Windows. Extract the zip file to a subfolder and run setup.exe and click on INSTALL. Close the window and connect the D1 mini module to your computer using a micro-USB cable
Start Arduino. Under menu File open Preferences and in Additional Boards Manager URLs enter:
https://arduino.esp8266.com/stable/package_esp8266com_index.json
Close this window with OK.
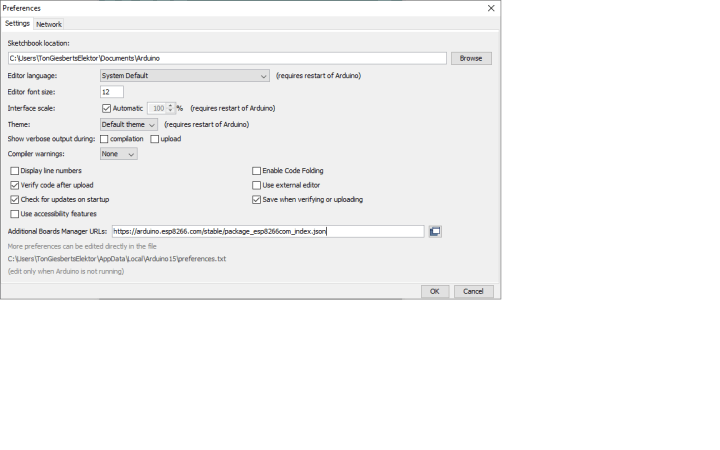
Open Tools – Board:…. and click on Boards Manager
In the entry field type esp8266
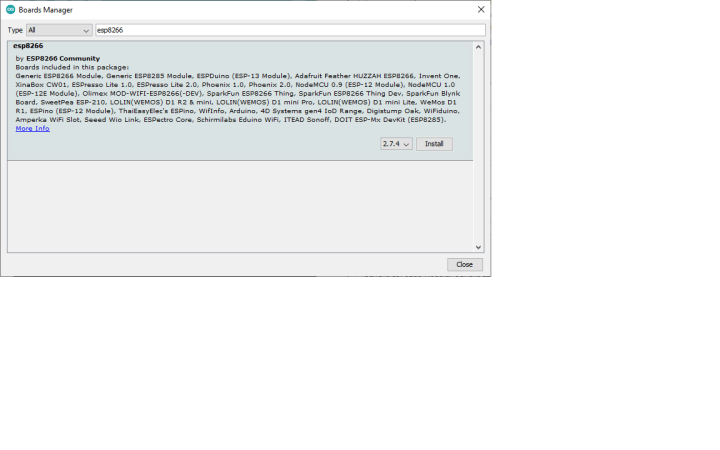
A version is displayed, the CO2-Guard was tested with 2.7.4. Click on ‘Install’. When finished installing click on ‘Close’.
In menu tools - Board: ...select in menu item ‘ESP8266 Boards (2.7.4)’ the board ‘LOLIN(WEMOS) D1 R2 & mini’. In menu ‘Tools’ following information should be visible.
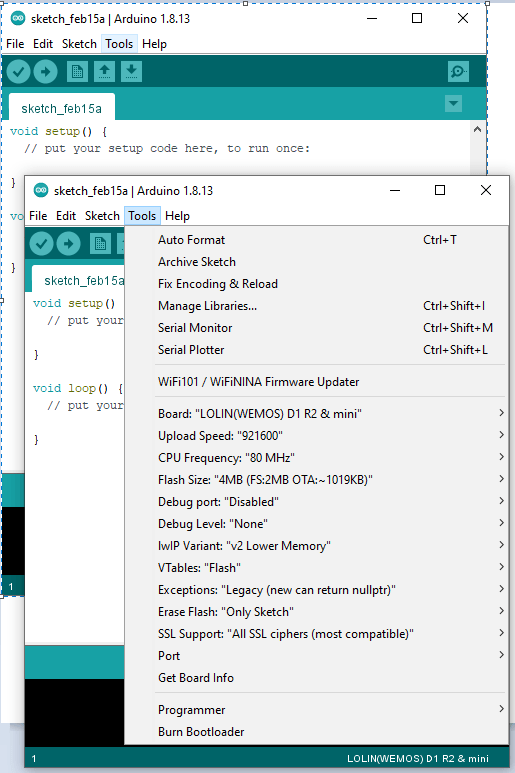
In menu Tools submenu Port select the COM port of the CH340 in de Device Manager (in our case it’s COM4). Close Arduino.
Upload program code
Download the file 210043-11.zip containing the Arduino sketch co2-guard.ino and file config.h and extract them to a subdirectory. Double click on co2-guard.ino, Arduino should open with the co2-guard sketch.
To compile and upload the code to the D1 mini click on the menu symbol for upload (arrow pointing to the right in the upper left corner.

ThingSpeak (create MathWorks account)
Visit the site: https://thingspeak.com/
Choose ‘Get Started For Free’. On the next page you have to create a MathWorks account (if you don’t already have one). Follow the instructions.
Or go to https://www.mathworks.com/mwaccount/register first.
After this create new channel (https://thingspeak.com/channels/new).

Enter the required data:
Name CO2_Guard
Description Monitor for CO2 levels with optical indication and acoustic alarm. Remote reading of CO2 level and temperature of sensor.
Field1 CO2
Field2 Temp
Tags CO2
Click on ‘Save Channel’
Now an overview of the channel just created is shown :
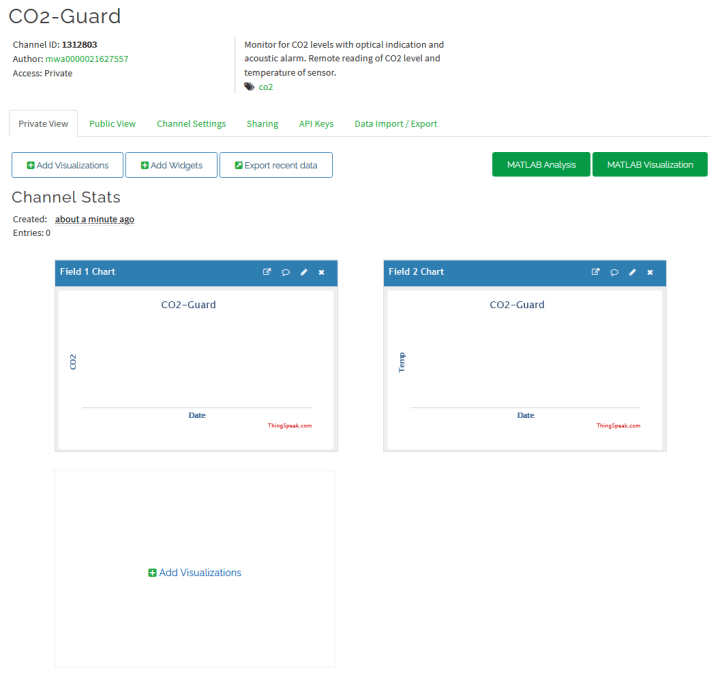
Now look under tab ‘API Keys’ and copy the Write API Key for later use. Keep it private and don’t show it to anyone else. Enter the Write API Key in the the config.h. Upload the software to the D1 mini and go to your ThingSpeak Account. Under menu Channels choose My Channels and then the tab Privat View. It should show something like this:
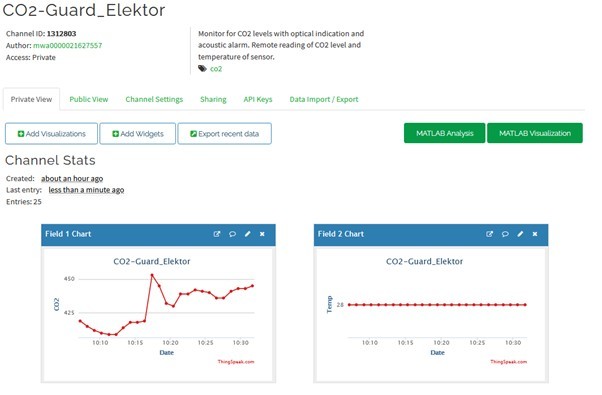
You can add individual users or make the channel public. That’s up to you. Individual users will get an email to the email address you entered under the tab Sharing (choice ‘Share channel view only with the following users:’):
Hi,
The ThingSpeak user, mwa……, has shared their ThingSpeak channel with you.
In order to view the channel, you will need to: Log in to www.ThingSpeak.com with the email address *** your email address*** and the password to your ThingSpeak account. If you do not have a ThingSpeak account with this email address, you may: Create a ThingSpeak account for free, or Request the author of the channel to share the channel with the email address listed on your ThingSpeak profile.Select the 'Channels Shared With Me' menu item from the 'Channels' menu in order to view this and other channels shared privately with you.Learn more or explore public channels on ThingSpeak to see examples of how other users use our service. Thank you,
The ThingSpeak Team
If someone shared a channel with you there’s a choice ‘Channels Shared With Me’ in your account:
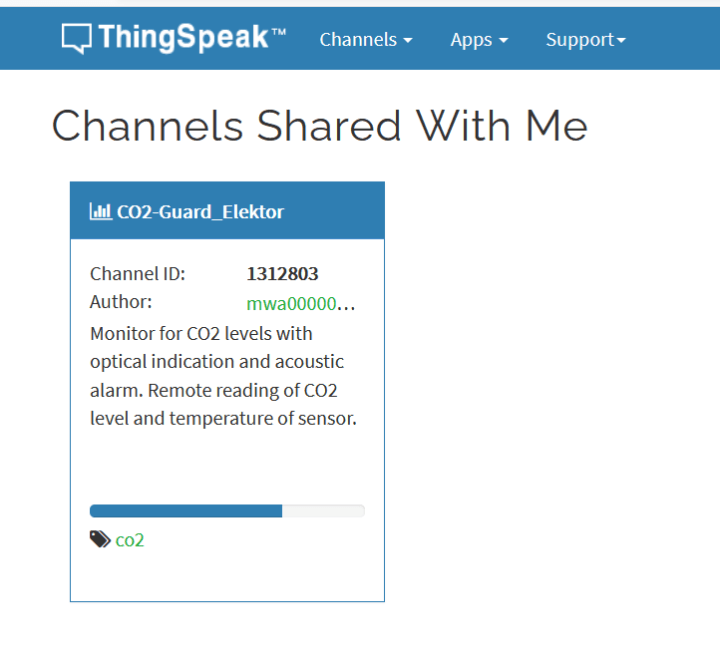
Software
At power-up the three LED's should blink simultaneously for a while and then the green LED and blue LED of the switch should light, when CO2 level is lower than 800 ppm. In the file config.h the SSID and password of your router must be entered to get a working Wi-Fi connection. Important: the software downloaded from our website uses dummy values. From that config.h:
#ifdef WLAN_SUPPORT
const char* ssid = "abc"; // enter your own SSID of Router
const char* password = "abc"; // enter your own WiFi password
String APIKey = "123"; // enter your own API-Key Thing Speak
#endif
Also the Write API Key has to be entered here. Replace the text string between “ “.
Important
Do not short circuit the 5 V output of a clone of the D1 mini, a diode in series with the 5 V from the USB, serving as a protection against an externally connected 5 V source, will most likely burn out and both 5V and 3.3 V are missing then (our experience). A fuse like on the Wemos version is missing here. Replace the diode or solder a small wire across it (remove the damaged diode first), but it won’t always help. Ports used by the circuit can be damaged. Some I/O’s of the ESP8266 can become unresponsive if not all of them. We found out the hard way. Although, in this specific case uploading software to the D1 mini board could still be done without a problem. Even flashing the firmware of the ESP8266EX chip can be done without errors but in our case didn’t help getting all I/O’s working again. Best is to replace the D1 mini then.Top overlay (copper bottom shown) of the single sided PCB of the CO2-Guard (210043-1 v1.1)
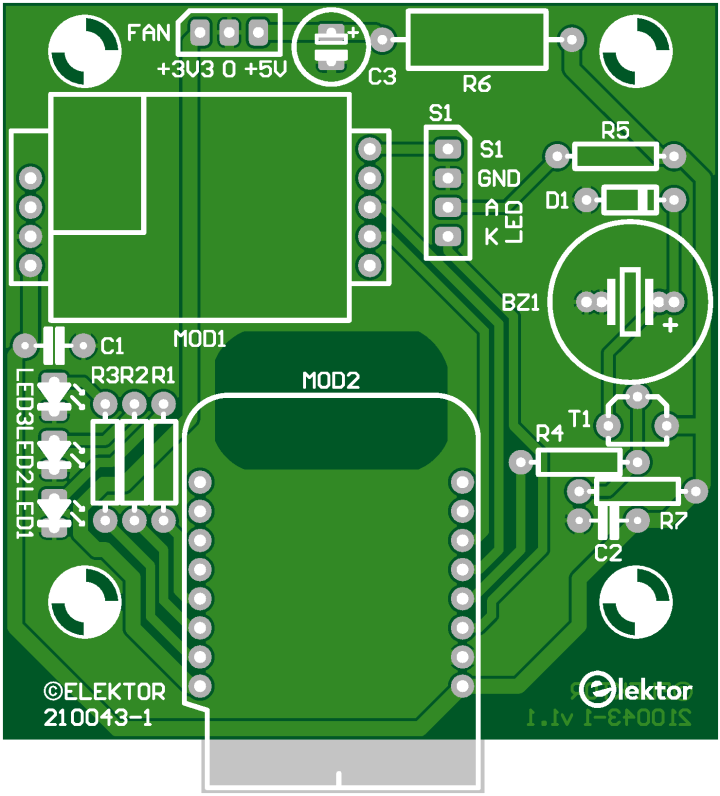
Bill of material CO2-Guard 210043-1 v1.1
| Resistor
| R1,R2,R3 = 330 Ω, 0.25 W, 5 %
| R4 = 4.7 kΩ, 0.25 W, 5 %
| R5 = 0 Ω, place wire, see text for more info
| R6 = 0 Ω, place wire for 5V or leave open, see text about value
| R7 = 1.5 kΩ, 0.25 W, 5 %
|
Capacitor
| C1,C2 = 100 nF, 50 V, 10 %, X7R, lead spacing 5 mm
| C3 = 100 µF, 25V, optional , not mounted, see text
|
| Semiconductor
| D1 = BAT85, DO-35
| T1 = BC327, PNP, TO-92
| LED1 = LED red, 5 mm
| LED2 = LED yellow, 5 mm
| LED3 = LED green, 5 mm
|
| Other
| MOD1 = 1x10 SIL header, female, split in 1x4 and 1x5 (*1)
| MOD1 = MH-Z19C, version 400-5000ppm, pins on bottom
| MOD2 = Wemos D1 mini
| MOD2 = 2 1x8 SIL header, male , 2 are part of D1 mini package
| S1 = switch+build-in LED (momentary on, self-reset, blue circle)
| Enclosure PP73BL, Supertronic
| BZ1 = DC buzzer, 5V, pitch 5 or 7.62 mm, diam. 14 mm max
| heat shrink tube, I.D 2.4 mm, 20 cm
| led housing, for 5 mm LED (LED1..3), Black
| FAN 5 VDC, 30x30x10.5 mm
| 12-pin male SIL header (separate in 3, 4, 5pens)
thin stranded wire to connect LED's and switch:
| stranded wire, 0.25 mm2, black, (2x8.5+12cm)
| stranded wire, 0.25 mm2, red, (8.5+12cm)
| stranded wire, 0.25 mm2, yellow, (12cm)
| stranded wire, 0.25 mm2, green, (12cm)
| stranded wire, 0.25 mm2, blue, (8.5cm)
|
Misc.
| PCB 210043-1 v1.1
KiCad Project
While the Projet is done in Altium, Mathias Claußen has already posted his progess on moving the design into KiCad.
While the project has been build and also PCBs have been ordered, please consider the KiCad project not as perfect and it is included for you to expore the PCB and also able to order it from a service you preffer. Also note that a Branch "Pinout_Update" now exists with an untested PCB. As I²C is not working with the remaining Pins the configuration has been swapped and a header for I²C is installed on this PCB revision.
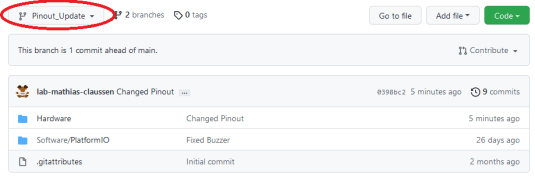
D1/D2 (I²C) connected to pinheader
D3/D4 RX/TX Sensor
D0 LED R
D7 LED G
D6 LED Y
D5 LED C
D8 Buzze
This shoudl allow for own I²C addons (e.g BME280 / BMP280 ) and sensors. Use this PCB at your own risk. It has not been tested.
Projectfiles can be found on GitHub
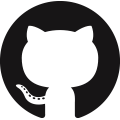
Discussie (9 opmerking(en))
NL0072254ID 3 jaar geleden
I'd be interested in joining the jumpstarter but it seems there is no way to do so? I am currently logged in to my Elektor account.
Thanks!
ElektorLabs 3 jaar geleden
NL0072254ID 2 jaar geleden
Thanks for the quick reply. Sorry to hear the kickstarter is over, it is slightly confusing that there is still a 'rocket' symbol and hints how to join. Maybe there can be some statement that the project campaign has ended.
See the screenshot I attached the last time what casued my confusion :)
Best regards!
HaSch 3 jaar geleden
I suggest connecting the cathode of LED C to D8 instead of D5. Then D5 would be free for the buzzer. However, you could also put the cathode of LED C permanently on GND, in my opinion it only has a decorative function anyway.
Mathias Clauszen 3 jaar geleden
a new revision with the following pinout has submitted for merging:
D1/D2 (I²C) connected to pinheader
D3/D4 RX/TX Sensor
D0 LED R
D7 LED C
D6 LED Y
D5 Buzzer
D8 LED G
Best Regards
Mathias_Claussen(Elektor) 3 jaar geleden
we are working on the new PCB to fix the pin-assignment. This may take some minutes to be done.
Best Regards
Mathias Claußen
HaSch 3 jaar geleden
Mathias Clauszen 3 jaar geleden
https://github.com/ElektorLabs/210043-CO2-Guard/issues/1
this should work better
HaSch 3 jaar geleden
Mathias Clauszen 3 jaar geleden
the changes are currently inside a pull-request and will be in the Elektor GitHub repository on monday if the admin will accept the pull-request. If you wan't to have a look already, check https://github.com/calm4git/210043-CO2-Guard/tree/New-Pinout as this is the source of the pull-request.
Regards
HaSch 3 jaar geleden
HaSch 2 jaar geleden
Here is the adapted FW to use with Arduino IDE (for BME280 sensor)
Have fun!
Hans
EDIT: Thanks to CalM for fixing the notes bug. I updated the version for latest PCB revision 2.4 and BME20 sensor. Here is version 2.4.1 of FW.
Mathias_Claussen(Elektor) 2 jaar geleden
thanks for the testrun and updated Firmware.
Best Regards
Mathias Claußen
HaSch 2 jaar geleden
-> Read EEPROM
-> SAVED CONF: CRC SAVED: 2697953792 <> CRC DATA 434755882
-> Do Failsave: Notes corrupt
Also, some font files aren't found:
-> Got request for: /css/basic.css
-> Content type: text/css
-> File /css/basic.css found
-> Got request for: /fonts/montserrat-v15-latin-regular.woff2
-> Content type: text/plain
-> File '/fonts/montserrat-v15-latin-regular.woff2' doesn't exist
-> Got request for: /fonts/montserrat-v15-latin-regular.woff
-> Content type: text/plain
-> File '/fonts/montserrat-v15-latin-regular.woff' doesn't exist
-> Got request for: /fonts/montserrat-v15-latin-regular.ttf
-> Content type: text/plain
-> File '/fonts/montserrat-v15-latin-regular.ttf' doesn't exist
-> Got request for: /fonts/montserrat-v15-latin-regular.svg
-> Content type: text/plain
-> File '/fonts/montserrat-v15-latin-regular.svg' doesn't exist
I didn't find the bug(s), maybe if somebody has a hint he's welcome.
Mathias Clauszen 2 jaar geleden
could you give me some hints on what Board Version you are using? Also which libary versions are used for the project?
For the missing Fonts files, some had to be stripped due to size and license issues and the webpages will fall back to browser default. Not nice but working according to spec.
For the EEPROM i will add some more debug info as it seems something is overwritung data in it.
Best Regards
CalM
Mathias Clauszen 2 jaar geleden
Best Regards
CalM
HaSch 2 jaar geleden
the notes bug seems not to be totally fixed. Indeed, the sketch doesn't produce that error message in console anymore. But if you restart the board the notes aren't stored. I think the problem is in routines eerwrite_notes() and eepread_notes() in datastore.cpp. It isn't enough to calculate you even have to write to and read from EEPROM.
Best regards
Hans
Mathias Clauszen 2 jaar geleden
the line 289 in datastore.cpp : eepwrite_struct( ( (void*)(¬es) ), sizeof(notes_t) , NOTES_START );
Sadly within the layout of the slash adresses are still overlaps in it. Need to shift some parts arround. New ZIP is attached
Best Regards
CalM
HaSch 2 jaar geleden
Are the functions write_credentials() and read_credentials() not necessary anymore?
Mathias Clauszen 2 jaar geleden
Regards
CalM
HaSch 3 jaar geleden
I did 2 additional firmware versions, one with integration of BME280 sensor for measuring ambient temperature (NOT sensor temperature of MH-Z19C sensor as in original firmware), pressure and humidity and the second one for a much cheaper BMP280 sensor. BMP280 sensor can only show temperature and pressure and is not as accurate as BME280. While BME280 is actually sold not under 16€ per piece BMP280 can be bought for about 2-3€ per piece.
For both versions it is necessary to do a light change of the PCB to get the sensors to work.
If someone is interested I can provide additional firmwares for download.
Best regards,
Hans
Mathias_Claussen(Elektor) 3 jaar geleden
if you like you can attach your Firmware under your post so we can add them into the downloads for the article. Also the changes can be backported into the platform.io firmware. Also note that a new PCB has been prepared and offers I²C access through a connector, but we had to change some pins for it. New version can be found on GitHub un the Branch "Pinout_Update". Details on new Pin configuration is at the end of the Labs article.
Best Regards
Mathias Claußen
HaSch 3 jaar geleden
here you can find my 2 versions of the firmware attached. Both are tested and working very well. I also added some lines in webserver index.html to work with these versions (are included in .zip files). So feel free to test. The code should work as it is.
I also added some information about PCB versions in the header of .ino files.
Best regards,
Hans
CO2Guard_BMP280.zip (62kb)
HaSch 3 jaar geleden
Dies ist ein sehr nützliches und gut ausgearbeitetes Projekt, was allerdings noch Luft nach oben hat. Auch ist es erforderlich, zunächst einmal einige Aussagen im Text oben gerade zu rücken. Zunächst einmal wäre da die beschriebene Prozedur für die Kalibrierung des Sensors mit Hilfe des Tasters. Angegeben ist, dass der Sensor zunächst für 20 Minuten einer Umgebung mit 400ppm CO2 ausgesetzt sein soll. Tut man das und drückt anschließend den Button für mindestens 7 Sekunden, wird der Referenz Level gespeichert. Dieser ist allerdings nicht 400ppm sondern 410ppm. Dadurch erreicht man, dass der übermittelte Wert plötzlich von 400ppm auf 410pp ansteigt. Korrekt wäre es, wenn die Anordnung 20 Minuten lang in einer Umgebung von 410ppm betrieben wird aber wer kann das schon?Zum zweiten liefert der Sensor MH-Z19C zwar Temperaturwerte, die in ThingSpeak dargestellt werden können, allerdings sind diese Werte wenig aussagekräftig. Wie man auch in der im Artikel dargestellten Abbildung sieht, sind diese Werte nämlich konstant, bei mir sind sie permanent 29°C. Vermutlich wird der Sensor auf Temperatur gehalten (wegen der Temperaturkompensation) und diese Werte übermittelt. Wenn man die Raumtemperatur ausgegeben haben will, liegt es nahe, einen weiteren Sensor in das Gehäuse einzubauen z.B. einen BME280, der neben der Temperatur auch noch die Luftfeuchtigkeit und den Luftdruck liefern kann. Dies ist allerdings mit einigen Hürden verbunden.Im Platinenlayout ist der CO2 Sensor über GPIO1 und GPIO2 mit dem D1 Mini verbunden. Dies ist gleichzeitig die I2C Schnittstelle des Microcontrollers, die der BME280 für die Kommunikation mit dem Board benötigt. Schade, dass diese schon belegt sind, obwohl dafür überhaupt keine Notwendigkeit besteht. Auf der anderen Seite sind nämlich GPIO16 und GPIO14 noch frei, die man auch für die Kommunikation mit dem MH-Z19C hätte nehmen können. Im PCB Entwurf hätten die Leiterbahnen ohne Überschneidungen entsprechend geroutet werden können.Mein erster Ansatz, den BME280 zu integrieren war es daher, die Pins GPIO16 und GPIO14 als I2C Schnittstelle zu nehmen und entsprechend umzudefinieren. Leider ist mir das bisher aus irgendeinem Grund noch nicht gelungen, vielleicht hat ja der ein oder die andere Leser/In noch eine Idee dazu.Was in jedem Fall funktionieren müsste wäre die PCB entsprechend abzuändern, die Leiterbahnen vom Sensor zum D1 Mini zu kappen und mit Drähten an die beiden anderen Pins des MC zu führen. Wenn ich mit meinen anderen Versuchen nicht weiterkomme, werde ich das ausprobieren.Wenn man den Einsatz der Schaltung in einem Büro oder einem Klassenraum plant, wäre es wünschenswert, wenn man z.B. LED Cluster anschließen könnte, wie sie in „richtigen“ Ampelanlagen eingesetzt werden. Dazu müsste noch etwas Elektronik auf die PCB gepackt werden damit die höheren Spannungen bzw. Ströme bereitgestellt werden können, die die LED Cluster benötigen. Auch wäre dafür ein eigenen Netzteil erforderlich. Selbstverständlich kann man die Elektronik auch in den externen Ampeln unterbringen (leicht sogar). Allerdings wäre auf der PCB die (entkoppelten) Anschlüsse dafür erforderlich.
Text in English language:
This is a very useful and well-developed project, but it still has room for improvement. It is also necessary to first set straight some statements in the text above. First of all, there is the described procedure for calibrating the sensor using the button. It is stated that the sensor should first be exposed to an environment with 400ppm CO2 for 20 minutes. If you do that and press the button after that for at least 7 seconds, the reference level is saved. However, this is not 400ppm but 410ppm. As a result, the transmitted value suddenly increases from 400ppm to 410pp. The correct way to do it would be to operate the Guard in an environment of 410ppm for 20 minutes, but who can do that?Second, the MH-Z19C sensor provides temperature values that can be displayed in ThingSpeak, but these values are not very meaningful. As you can also see in the figure shown in the article, these values are constant, for me they are permanently 29°C. The sensor is probably kept at temperature (because of the temperature compensation) and these values are transmitted. If you would like to transmit the room temperature it makes sense to install another sensor in the housing, e.g. a BME280, which can also provide the humidity and air pressure in addition to the temperature. However, this comes with a few hurdles.In the PCB layout, the CO2 sensor is connected to the D1 Mini via GPIO1 and GPIO2. This is also the microcontroller's I2C interface, which the BME280 needs to communicate. It is a pity that these are already taken, although there is no need for it at all. On the other hand, GPIO16 and GPIO14 are still unused, which could also have been taken for communication with the MH-Z19C. In the PCB design, the traces could have been routed accordingly without overlapping.My first approach to integrate the BME280 was therefore to take pins GPIO16 and GPIO14 as I2C interfaces and redefine them accordingly. Unfortunately, for some reason I haven't been able to do that yet, maybe one or the other reader has an idea.What would have to work in any case would be to change the PCB accordingly, cut the traces from the sensor to the D1 Mini and run wires to the other two pins of the MC. If I get stuck with my other attempts, I'll try this.If you plan to use the circuit in an office or a classroom, it would be desirable if you could, for example, connect LED clusters like those used in “real” traffic lights. To do this, some electronics would have to be packed on the PCB so that the higher voltages or currents that the LED clusters require can be provided. A separate power supply unit would also be required for this. Of course, the electronics can also be accommodated in the external traffic lights (easily even). However, the (decoupled) connections for this would be required on the PCB.
Mathias_Claussen(Elektor) 3 jaar geleden
With kind regards
Mathias Claussen
HaSch 3 jaar geleden
Wire.begin(14,12);
#define LEDred 16
That works.
Mathias_Claussen(Elektor) 3 jaar geleden
Best Regards
Mathias Claußen
HaSch 3 jaar geleden
HaSch 3 jaar geleden
Mathias_Claussen(Elektor) 3 jaar geleden
Best Regards
Mathias Claußen
HaSch 3 jaar geleden
Mathias Clauszen 3 jaar geleden
thanks for the upload of the ArduinoIDE Version. Thi will also make it easy for those who use the Arduino IDE.
I guess you are still usingi the LitteFS and requiere https://github.com/earlephilhower/arduino-esp8266littlefs-plugin to be installed?
Best Regards
CalM
HaSch 3 jaar geleden
First of all you have to disable wdt in setup: After that you should feed it in main loop: That may work in your case but not in all. With this command you disable the soft wdt but not the hard wdt. Hard wdt can not be disabled and so, you should feed it. But how?
Mathias Clauszen 3 jaar geleden
problem is more the way the loop is done and never returning. WDT is usally feed if retunrning from the loop() function and here is it simply not done. New Software is on its way.
Best Regards
M.C.
HaSch 3 jaar geleden
if you work on the software, it would be great if you implement WifI manager. It will make the project more universal.
And another suggestion for the PCB: For the use in larger rooms like classrooms or office spaces it would be very useful if there were a possibility to connect LED clusters that need more voltage or/and current to make the display more noticeable.
Best regards,
Hans
Mathias Clauszen 3 jaar geleden
WiFi Manger is possible to implement. For the display, the way the hardware and pinout was done by the author has many areas where it can be improved. For driving large matrix displays the ESP8266 using GPIOs is not the best choise (not many IOs). As the basic schematic is done by an author / other person there is not much that i'm allowed to change currently. As the Project is now transfered into KiCad ( https://twitter.com/ElektorMathias/status/1471403317620269059 ) this could be done up on request :-) . Also may the enclosure gets a 3D printable version later on.
Best Regards and happy holydays
Mathias Claußen
HaSch 3 jaar geleden
call to 'HTTPClient::begin' declared with attribute error: obsolete API, use ::begin(WiFiClient, url)
What's going wrong? I set correct WiFi credentials and write API in config.h
EDIT: The error only occurs if you use the latest version of ESP32 board manager file. If using 2.7.4 all is fine. I suggest to make some changes to the sketch to make it work with newest board file.
HaSch 3 jaar geleden
HaSch 3 jaar geleden
Mathias_Claussen(Elektor) 3 jaar geleden
files can be found at: https://github.com/ElektorLabs/210043-CO2-Guard
Be aware that a testrun for the KiCad version is currently (due to part shortage) not been done.
Best Regards
Mathias Claußen
Content Director, Elektor 3 jaar geleden
Thanks!
Mathias_Claussen(Elektor) 3 jaar geleden
Best Regards
Mathias Clauszen 3 jaar geleden
Best Regards
M.C.
Robert Waldvogel 3 jaar geleden
Where can I get the circuit board? Or as a whole kit?
ElektorLabs 3 jaar geleden
Robert Waldvogel 2 jaar geleden
Mathias_Claussen(Elektor) 2 jaar geleden
HaSch has tested the last KiCad Revision 2.4 of the PCB and it seems the bugs are worked out with this one. You can use aisler.net if you want to order your PCBs yourself. Within Germany 3 boards would be 14 Euros including shipping.
Best Regards
Mathias Claußen
HaSch 2 jaar geleden
Robert Waldvogel 2 jaar geleden
Small additional question: Which buzzer is suitable? Type ?
co2.png (593kb)
Mathias_Claussen(Elektor) 2 jaar geleden
For the buzzer a WT-1205 by Soberton Inc. would fit.
Best Regards
Mathias Claußen
HaSch 2 jaar geleden
I understand your confusion. The reason for adding a footprint for an I2C sensor as BME280 or BMP280 was that transmitted temperature values of MH-Z19C sensor to ThingSpeak as described in article above made absolutely NO sense. Because these values are only constant values of sensor heating with NO information about room temperature.
As D1 mini had 2 pins unused it was obvious to use it for a real environment sensor as BME280 or BMP280.
If you are NOT planning to use such a sensor be aware to use the right firmware. FW with BME280/BMP280 support will check if such a sensor is present and will produce an error message if not.
Best regards,
Hans Schneider
HaSch 2 jaar geleden
You can use any DC buzzer without built-in electronics, 5V, pitch 5 or 7.62 mm, diameter 14 mm maximal. These buzzers are not able to produce it's own tone. You can check while connecting to a battery. If it produces a tone it's not the right one.