Magnetic Motion Machine

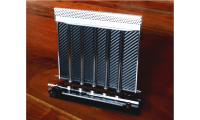
Some of you will have a gadget on your desk, such as a Newton pendulum. This project shows a machine that moves small magnets in acrylic glass tubes, with adjustable speed and movement patterns. Of course, appropriate lighting should not be missing.
You're sure to find one or two gadgets on your desk, like the well-known Newton pendulum, which allows various movement sequences and encourages play, etc.
Now I've tidied up again and found various acrylic glass tubes in different sizes and thought about what I could do with them as they are just too good to throw away. As luck would have it, I also came across a box with neodymium power magnets of various sizes.
And then it started rattling in my head. The smallest magnets fit exactly into the smallest acrylic glass tube and could be moved back and forth perfectly. Now the idea came to me to move these magnets automatically and reminded me of experiments with a small 5 volt electromagnet that had been done a long time ago. So I had some of these electromagnets delivered to me and, based on the Newton pendulum, I came up with a similar design, but based on acrylic glass tubes. I placed the small electromagnets under the tubes arranged vertically next to each other. My thought was that if the polarity was correct, the magnets would be repelled by the electromagnets and move upwards. If the individual magnets are controlled accordingly, different movement patterns should be able to be generated, although the speed of this movement should also be variable. Voila, the idea was born, all that was missing was the practical implementation.
In order to accommodate the control electronics as inconspicuously as possible, I decided to use the small Arduino Nano. When it came to electromagnets, I chose the SEN-MAG25N type, which is designed for 5 volts and already contains a MOSFET including a protective diode, so I no longer had to worry about controlling the solenoid coil. The construction was therefore quite simple and most of the work went into the mechanical construction of this 'machine'.
Since it is a eye catcher that should also meet optical requirements, appropriate lighting was also used. Here I chose blue LEDs, which were supposed to illuminate the individual tubes. These should light up at the same time as the activated magnet.
Since the deflection of the magnets had to be strong, their mass had to be as low as possible. Magnets with a diameter of 4 mm and a length of 5 mm were used. The acrylic glass tubes used also had an inner diameter of 4 mm. My original skepticism that the diameter might be too small turned out to be unfounded. The magnets could be moved perfectly in the tubes.
Now it was time to develop the software. The first thing I thought about was interesting movement patterns. After various experiments, I decided on four movement patterns, which can be selected by pressing a button. In order to be able to change the movement pattern at any time during the program run, the button query is interrupt-controlled. The movement speed is adjusted using a potentiometer, which supplies the appropriate voltage to one of the AD converters. To stop the movement of the magnets, all you have to do is turn the potentiometer all the way to the left.
Five electromagnets are used in my design. Since the current consumption of an electromagnet can be up to 500 mA according to the data sheet, the power supply used should be able to deliver 3 A in order to be able to handle the Arduino Nano's approximately 150 mA. However, the movement patterns I programmed lead to an average current consumption of less than 2 A. Since the Arduino Nano works reliably from 6 volt input voltage, a stabilized 6 volt 3 amp power supply should be sufficient for operation. In order not to overload the electromagnets, the operating voltage required for this is reduced to a healthy level using two P 600A diodes connected in series.
Another thing about the structure: as the first attempts turned out, they are used neodymium magnets so strong that no matter which direction they were placed on the activated electromagnet, they were not repelled and remained firmly attached to the iron core. To solve this problem, I stuck a strip of felt about 3 mm thick over the electromagnets, which at the same time reduced the noise emissions to a comfortable level.
Since I haven't found such a machine even after a long search on the Internet, I can well imagine that commercial marketing by Elektor could make sense. This gadget is definitely a highlight on the desk. Once you start playing with it, you won't let go of it anytime soon. Even my wife, who is not particularly tech-savvy, likes to pass the time and listen to the rhythmic clacking of the magnets. Depending on the speed set, interesting visual and acoustic effects can be achieved with every movement pattern.
An expansion is also conceivable, such as expanding the number of magnets and programming new movement sequences - there are no limits to your imagination.
So that you can get an idea of how it works, I have linked a short video on YouTube.
Now I've tidied up again and found various acrylic glass tubes in different sizes and thought about what I could do with them as they are just too good to throw away. As luck would have it, I also came across a box with neodymium power magnets of various sizes.
And then it started rattling in my head. The smallest magnets fit exactly into the smallest acrylic glass tube and could be moved back and forth perfectly. Now the idea came to me to move these magnets automatically and reminded me of experiments with a small 5 volt electromagnet that had been done a long time ago. So I had some of these electromagnets delivered to me and, based on the Newton pendulum, I came up with a similar design, but based on acrylic glass tubes. I placed the small electromagnets under the tubes arranged vertically next to each other. My thought was that if the polarity was correct, the magnets would be repelled by the electromagnets and move upwards. If the individual magnets are controlled accordingly, different movement patterns should be able to be generated, although the speed of this movement should also be variable. Voila, the idea was born, all that was missing was the practical implementation.
In order to accommodate the control electronics as inconspicuously as possible, I decided to use the small Arduino Nano. When it came to electromagnets, I chose the SEN-MAG25N type, which is designed for 5 volts and already contains a MOSFET including a protective diode, so I no longer had to worry about controlling the solenoid coil. The construction was therefore quite simple and most of the work went into the mechanical construction of this 'machine'.
Since it is a eye catcher that should also meet optical requirements, appropriate lighting was also used. Here I chose blue LEDs, which were supposed to illuminate the individual tubes. These should light up at the same time as the activated magnet.
Since the deflection of the magnets had to be strong, their mass had to be as low as possible. Magnets with a diameter of 4 mm and a length of 5 mm were used. The acrylic glass tubes used also had an inner diameter of 4 mm. My original skepticism that the diameter might be too small turned out to be unfounded. The magnets could be moved perfectly in the tubes.
Now it was time to develop the software. The first thing I thought about was interesting movement patterns. After various experiments, I decided on four movement patterns, which can be selected by pressing a button. In order to be able to change the movement pattern at any time during the program run, the button query is interrupt-controlled. The movement speed is adjusted using a potentiometer, which supplies the appropriate voltage to one of the AD converters. To stop the movement of the magnets, all you have to do is turn the potentiometer all the way to the left.
Five electromagnets are used in my design. Since the current consumption of an electromagnet can be up to 500 mA according to the data sheet, the power supply used should be able to deliver 3 A in order to be able to handle the Arduino Nano's approximately 150 mA. However, the movement patterns I programmed lead to an average current consumption of less than 2 A. Since the Arduino Nano works reliably from 6 volt input voltage, a stabilized 6 volt 3 amp power supply should be sufficient for operation. In order not to overload the electromagnets, the operating voltage required for this is reduced to a healthy level using two P 600A diodes connected in series.
Another thing about the structure: as the first attempts turned out, they are used neodymium magnets so strong that no matter which direction they were placed on the activated electromagnet, they were not repelled and remained firmly attached to the iron core. To solve this problem, I stuck a strip of felt about 3 mm thick over the electromagnets, which at the same time reduced the noise emissions to a comfortable level.
Since I haven't found such a machine even after a long search on the Internet, I can well imagine that commercial marketing by Elektor could make sense. This gadget is definitely a highlight on the desk. Once you start playing with it, you won't let go of it anytime soon. Even my wife, who is not particularly tech-savvy, likes to pass the time and listen to the rhythmic clacking of the magnets. Depending on the speed set, interesting visual and acoustic effects can be achieved with every movement pattern.
An expansion is also conceivable, such as expanding the number of magnets and programming new movement sequences - there are no limits to your imagination.
So that you can get an idea of how it works, I have linked a short video on YouTube.
Updates van de auteur
JoergT 1 jaar geleden
JoergT 1 jaar geleden