Wagon top coal sampling Remote EPB Module
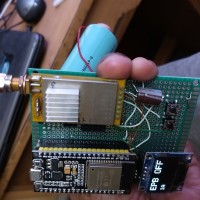
Wagon top coal sampling itself is a hazard when you have to collect samples from a long 500 meter windy rail road and more than 100 wagons per day!
Wagon top coal sampling Remote EPB Module
More than 1 lakh [= 100,000, ed.] tons of coal to unload everyday involving 27 rakes and 60 wagons per rake is a gigantic nature of activities everyday. Also, why it should not be like that when you are running one of the largest thermal power plants of the country! More than a dozen units with billions of units of electricity generating everyday!
However, coal comes from the nearby mines through merry-go-round systems. Every rake needs to be sampled for coal calorific value and for that matter nearly a dozen wagons per rake (a rake consists about 58 to 60 wagons) needs to be sampled for wagon-top.
A man needs to climb the wagon top and collect wagon-top samples. Series of high mount special sampling racks are fabricated on the rail side and kept at strategic spots where the sample man climbs and then collect samples from wagon top.
Immediately after collection, the sample is grinned and then mixed thoroughly & sent to the chemistry laboratory for calorific value analysis. The CV [Calorific Value] of total moisture of the arrived coal is one of the most important parameters of the power plant operation. Crores [1 crore equals 10,000,000, ed.] of money is involved for even a one kilo calory change in the CV of the coal. The whole operation needs to be done under close supervision right from sample collection upto the publishing of the data and every power generating company does it very seriously.
Immediately after collection of samples it is to be crushed, thoroughly mixed and then made into samples. It has been seen that on a few occasions while collecting samples the rake below rolled inadvertently causing accidents when the man on wagon top falls or gets wounded due to movement of the rake. Even fatal accidents are not unknown for similar incidents.
As per standard, every high table is required to be attached with an EPB [Emmergency Push Button] which will be connected with the signaling system such that once the sampling man is on the table, he will press the push button, which will change the signal to red or green.
As the number of wagons per rake is increased multi fold to improve the throughput of coal receipt, sometimes the farthest sampling table needed to be located as far as 500 meters away from the engine. The wiring for such long portion poses a big issue for these far-away sampling tables. Many times the rail also takes curvatures causing complete hindrance to the visual of the signal lights.
We first thought of adding an audio alarm when the EPB is pressed by the signal man, which will be heard from the farthest post as a feedback that his EPB signal has hit home! But when the BOBRN [Bottom Open Bottom Rapid discharge with Pneumatic system] wagons unloads the coal onto the hoppers attached below the rake, the sound is enough to hide any background alarm.
Next it was thought to provide a feedback signal at the each EPB unit but the amount of feedback wiring from the breaker upto the EPB is very difficult to achieve. Same way it was thought to increase the height of the signal mast so that it can be visible from distance but all went for a toss. The congregation of 4 lines with curvatures before the hoppers, make them very confusing to identify for which line it would be from afar. … and this project was born.
EPB sender: This is a small LiPo single cell-operated, exact replica of the EPB unit with one small antenna and a small OLED screen. There are two push-to-on buttons. When the top button is pressed, it sends a highly encrypted signal to the remote receiver unit, situated in the control cabin room. It operates two relays – one for the EPB operation and other for the release of the EPB operation [RED or GREEN signal]. On every successful operation, the receiver unit will send a confirmation signal back to the sender unit which will be relayed on the OLED screen.
EPB signal receiver unit: This unit runs on 3.3 volts and remains alert for the signal issued by the respective EPB sender unit. On receiving of the signal, it will energize GPIO [15 or any other of your choice ] which in turn runs a relay contract and returns a message [1A or anything of your choice] for the sender unit. Same way when the other button is pressed on the sender unit , the GPIO [12 or any other of your choice] will energize which in turn will run a relay contract and returns a message [2B or anything of your choice] for the sender unit. When one GPIO becomes on the other one becomes off invariably.
Return Feedback: On receiving of the return signal [1A or 2B] ,it will appear on the OLED attached with the sender unit. The sender unit will then come to know for sure whether his command has hit home or not.
Security: To have improved security such that the system never gets operated by any outside signal from anywhere, we have selected the Ebyte made transceivers which is to be hardcrypted by three parameters – channel frequency, air rate and a 4 byte ID. If all these three parameters are same, then only the pair will communicate with each other. The chip communicates on SS mode and on 500 mw [27 dbM] & 868 MHz, it can travel 500 meter very comfortably on the railway track with a small handheld antenna and the receiver unit antenna is placed on the roof top of the cabin / control room so that it remains in sight everywhere.
Prototype: Handheld EPB unit [sender] Operation: This is very straight forward. The EPB of the sender unit is pressed. It sends EPB signal to the remote unit whose antenna is situated at a higher elevation. It receives signal, actuates the related signal and then sends a confirmation to the sender unit, which gets displayed on the small OLED attached with the sender unit. When the requirement is over the , the sender unit press the EPB release button [the other push button] which will release the signal. In case the system is not available, or the signaling EPB is kept bypassed for operational purpose, the feedback signal will never reach to the sender unit, thus he gets alerted which will eventually avoid miss communications.
Cost: Approx $USD 100 for the electronics.
Present status: We are now doing field testing. At the beginning we provided [Receiver unit] alarm to the loco pilot dashboard with a stick antenna projected out of the driver cabin. The LED signal is converted into an audio alarm system for the loco pilot. For feedback signal the loco pilot has to press two EPBs to create the 1A and or 2B return message for the sender.
In the next phase this system will be shifted to the control cabin where the signal control feedback [Red or Green light signal] will be used to create the 1A and or 2B feedback signal. The incoming LEDs will alarm the operator to operate the signal accordingly [Red or Green]
Still many things to be fine tuned to integrate it with the signaling [S&T] system. However, the basic will start with this unit and this idea only.
Software: attached herewith.
Bye, bye
S. Bera Vindhyanagar
More than 1 lakh [= 100,000, ed.] tons of coal to unload everyday involving 27 rakes and 60 wagons per rake is a gigantic nature of activities everyday. Also, why it should not be like that when you are running one of the largest thermal power plants of the country! More than a dozen units with billions of units of electricity generating everyday!
However, coal comes from the nearby mines through merry-go-round systems. Every rake needs to be sampled for coal calorific value and for that matter nearly a dozen wagons per rake (a rake consists about 58 to 60 wagons) needs to be sampled for wagon-top.
A man needs to climb the wagon top and collect wagon-top samples. Series of high mount special sampling racks are fabricated on the rail side and kept at strategic spots where the sample man climbs and then collect samples from wagon top.
Immediately after collection, the sample is grinned and then mixed thoroughly & sent to the chemistry laboratory for calorific value analysis. The CV [Calorific Value] of total moisture of the arrived coal is one of the most important parameters of the power plant operation. Crores [1 crore equals 10,000,000, ed.] of money is involved for even a one kilo calory change in the CV of the coal. The whole operation needs to be done under close supervision right from sample collection upto the publishing of the data and every power generating company does it very seriously.
Immediately after collection of samples it is to be crushed, thoroughly mixed and then made into samples. It has been seen that on a few occasions while collecting samples the rake below rolled inadvertently causing accidents when the man on wagon top falls or gets wounded due to movement of the rake. Even fatal accidents are not unknown for similar incidents.
As per standard, every high table is required to be attached with an EPB [Emmergency Push Button] which will be connected with the signaling system such that once the sampling man is on the table, he will press the push button, which will change the signal to red or green.
As the number of wagons per rake is increased multi fold to improve the throughput of coal receipt, sometimes the farthest sampling table needed to be located as far as 500 meters away from the engine. The wiring for such long portion poses a big issue for these far-away sampling tables. Many times the rail also takes curvatures causing complete hindrance to the visual of the signal lights.
We first thought of adding an audio alarm when the EPB is pressed by the signal man, which will be heard from the farthest post as a feedback that his EPB signal has hit home! But when the BOBRN [Bottom Open Bottom Rapid discharge with Pneumatic system] wagons unloads the coal onto the hoppers attached below the rake, the sound is enough to hide any background alarm.
Next it was thought to provide a feedback signal at the each EPB unit but the amount of feedback wiring from the breaker upto the EPB is very difficult to achieve. Same way it was thought to increase the height of the signal mast so that it can be visible from distance but all went for a toss. The congregation of 4 lines with curvatures before the hoppers, make them very confusing to identify for which line it would be from afar. … and this project was born.
EPB sender: This is a small LiPo single cell-operated, exact replica of the EPB unit with one small antenna and a small OLED screen. There are two push-to-on buttons. When the top button is pressed, it sends a highly encrypted signal to the remote receiver unit, situated in the control cabin room. It operates two relays – one for the EPB operation and other for the release of the EPB operation [RED or GREEN signal]. On every successful operation, the receiver unit will send a confirmation signal back to the sender unit which will be relayed on the OLED screen.
EPB signal receiver unit: This unit runs on 3.3 volts and remains alert for the signal issued by the respective EPB sender unit. On receiving of the signal, it will energize GPIO [15 or any other of your choice ] which in turn runs a relay contract and returns a message [1A or anything of your choice] for the sender unit. Same way when the other button is pressed on the sender unit , the GPIO [12 or any other of your choice] will energize which in turn will run a relay contract and returns a message [2B or anything of your choice] for the sender unit. When one GPIO becomes on the other one becomes off invariably.
Return Feedback: On receiving of the return signal [1A or 2B] ,it will appear on the OLED attached with the sender unit. The sender unit will then come to know for sure whether his command has hit home or not.
Security: To have improved security such that the system never gets operated by any outside signal from anywhere, we have selected the Ebyte made transceivers which is to be hardcrypted by three parameters – channel frequency, air rate and a 4 byte ID. If all these three parameters are same, then only the pair will communicate with each other. The chip communicates on SS mode and on 500 mw [27 dbM] & 868 MHz, it can travel 500 meter very comfortably on the railway track with a small handheld antenna and the receiver unit antenna is placed on the roof top of the cabin / control room so that it remains in sight everywhere.
Prototype: Handheld EPB unit [sender] Operation: This is very straight forward. The EPB of the sender unit is pressed. It sends EPB signal to the remote unit whose antenna is situated at a higher elevation. It receives signal, actuates the related signal and then sends a confirmation to the sender unit, which gets displayed on the small OLED attached with the sender unit. When the requirement is over the , the sender unit press the EPB release button [the other push button] which will release the signal. In case the system is not available, or the signaling EPB is kept bypassed for operational purpose, the feedback signal will never reach to the sender unit, thus he gets alerted which will eventually avoid miss communications.
Cost: Approx $USD 100 for the electronics.
Present status: We are now doing field testing. At the beginning we provided [Receiver unit] alarm to the loco pilot dashboard with a stick antenna projected out of the driver cabin. The LED signal is converted into an audio alarm system for the loco pilot. For feedback signal the loco pilot has to press two EPBs to create the 1A and or 2B return message for the sender.
In the next phase this system will be shifted to the control cabin where the signal control feedback [Red or Green light signal] will be used to create the 1A and or 2B feedback signal. The incoming LEDs will alarm the operator to operate the signal accordingly [Red or Green]
Still many things to be fine tuned to integrate it with the signaling [S&T] system. However, the basic will start with this unit and this idea only.
Software: attached herewith.
Bye, bye
S. Bera Vindhyanagar
Discussie (1 opmerking(en))